PheasantHunter
ArboristSite Member
After lots of lurking on this site and some free hand milling. I finally built my first mill. I say first as I am already thinking about thinks I would do differently. The saw is a 390, also my first milling saw, I would like to upgrade to something larger...of course!
I had a half log of mesquite that I brought back from Oklahoma last year for my first milling. I stored it in plastic outside under a bunch of sawdust (no checking and still solid) . The mill worked fine, however, more overhang on the backside of it would be good. I am still working on "spacers", the minimum cut with this mill would be 1 1/8" which I would plan to do very often, prefer 2" most of the time. Cost to build the mill was less than $20.
Open to suggestions on the mill and/or milling.
I had a half log of mesquite that I brought back from Oklahoma last year for my first milling. I stored it in plastic outside under a bunch of sawdust (no checking and still solid) . The mill worked fine, however, more overhang on the backside of it would be good. I am still working on "spacers", the minimum cut with this mill would be 1 1/8" which I would plan to do very often, prefer 2" most of the time. Cost to build the mill was less than $20.
Open to suggestions on the mill and/or milling.
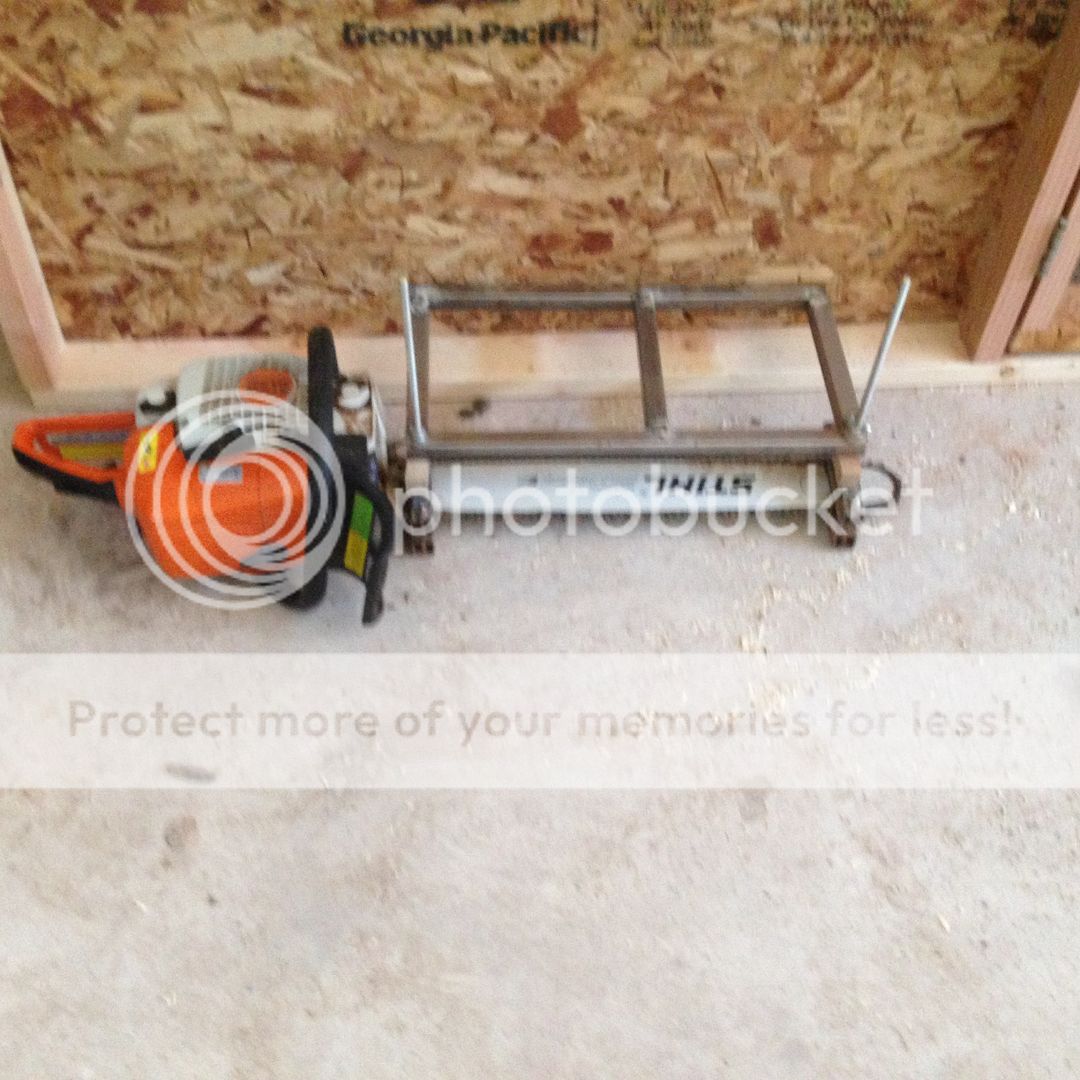
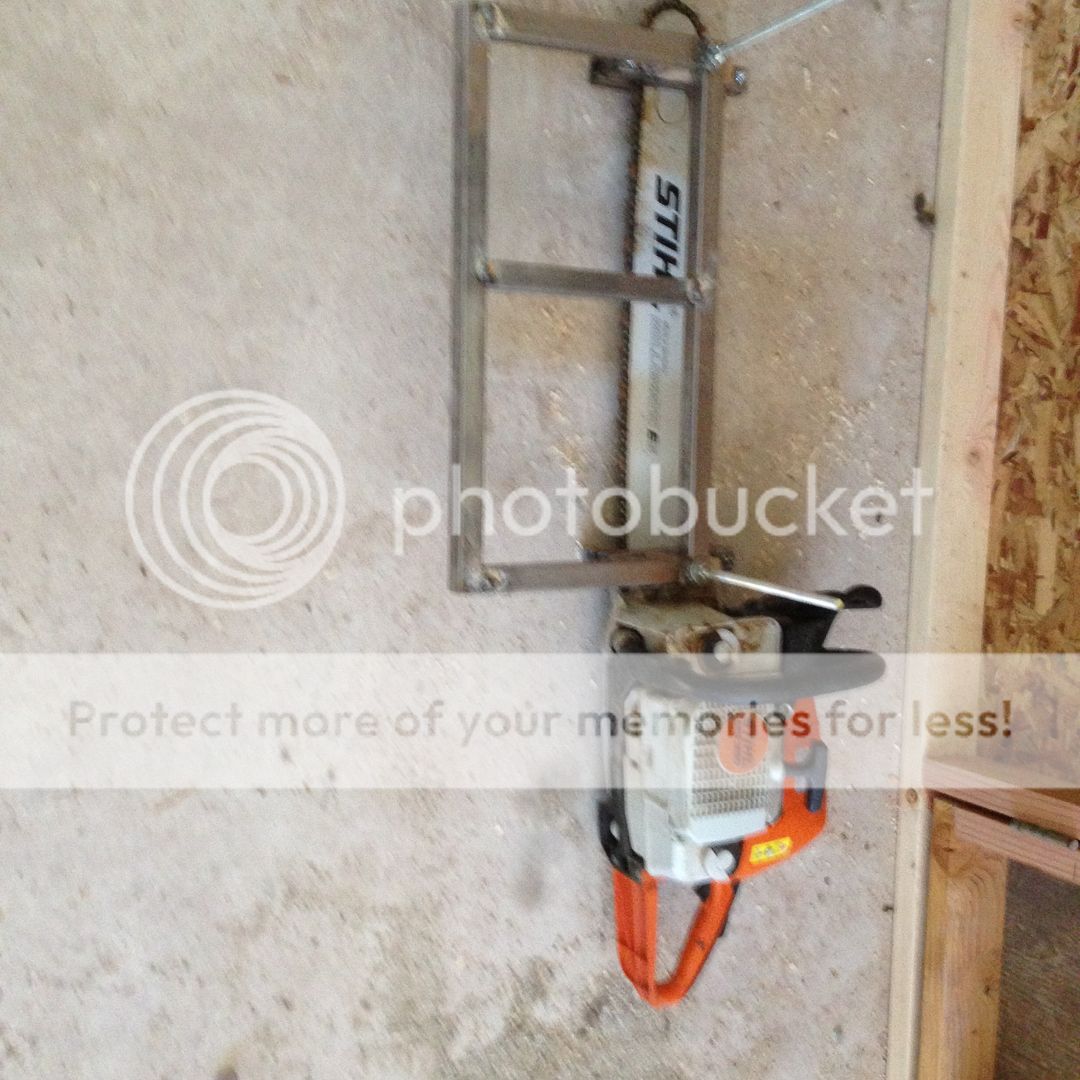
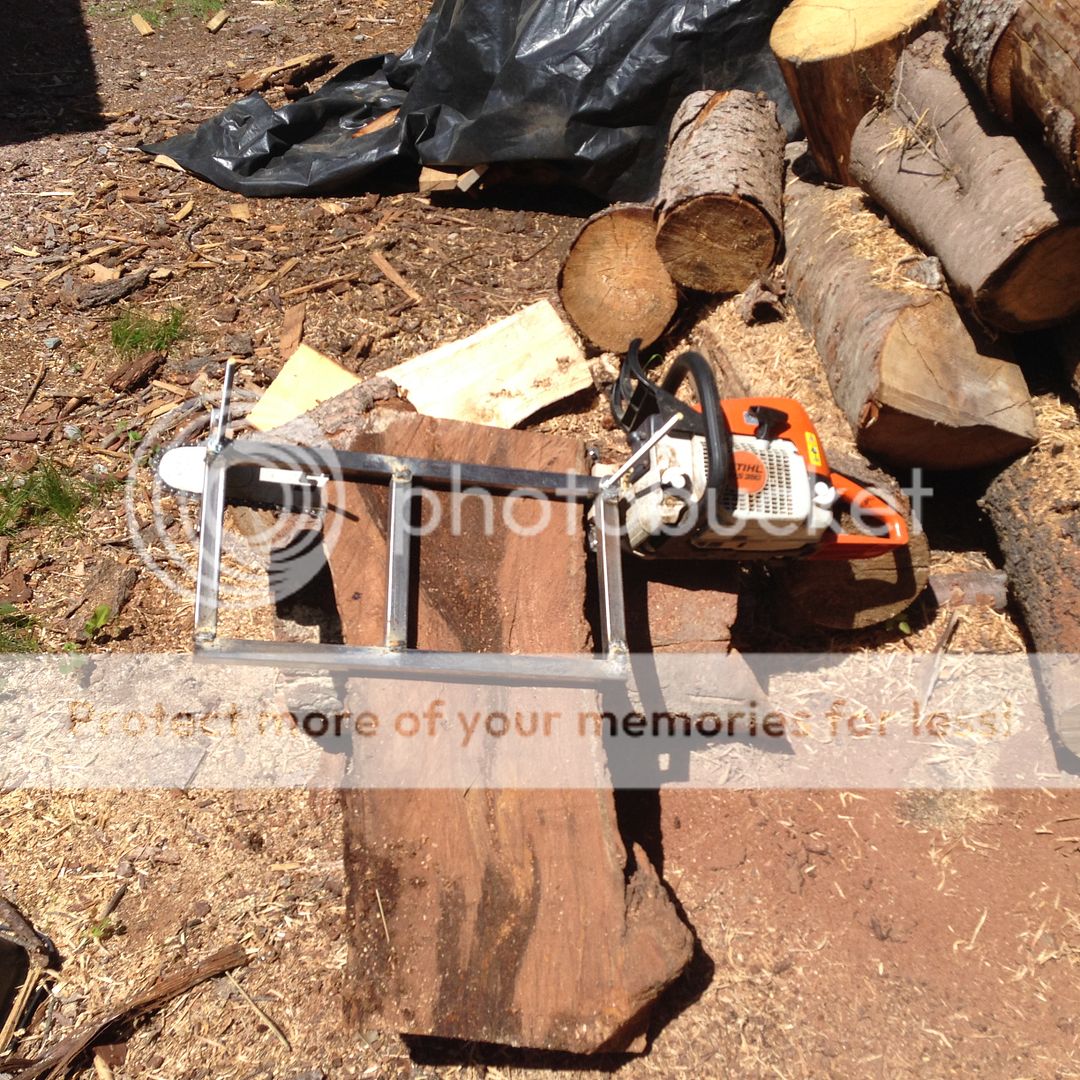
