markvanzee
ArboristSite Member
dear milling friends,
I have started a new project lately, I've bought a beech logs that measures 1.85 meter/ 73'' at the butt and is 5 meters long (196'') It weights 9.5 tons. I have been chainsaw milling since i was 18, so a couple of years of experience but this is my largest log so far. but i only cut maybe 2 logs a year because I don't really have the space to mill the logs. but gladly my employer let me delivery this log to my work so I can mill it there. this really helps because I can also use all the equipment; forklifts, woodworking/metalwork equipment.
[/IMG]
stihl880 with 48'' for scale
I have a 42'' alaskan style mill but logosol/stihl (the red frame) with a 48'' bar and i have a logosol big mill basic system. But I have always been intrigued by the dual head milling setups. and since I usually cut slabs for table tabs etc. I have had a couple situations were I have been slabbing freehand because my other mill couldn't handle the logs.
so I've started making a new dual-headed mill. this will run a 87'' bar, with 404 stihl ripping chain. I've constructed the mill with aluminium profiles 40 x 80 mm, and made the rest out of metal. i've used the existing holes in the bar to mount the bar to the mill. I figured this was better than bar clamps since this would allow me to remove the chain for sharpening easiers. for this reason I also plan on running without clutch cover. only a clamp plate. I will add another safety guard so don't worry..
the big problem that occurs with these long bars is bar sag. I have fitted a couple plates to tension the bar, this seems to work, at first the bar had sagged quite a bit even with the 2 powerheads. but I was able to remove this sag with the adjustment bolts.
I plan on making 2 U-shaped guide shoes under the mill to run over rails. I have aluminium 100x100 rails to run over. I have a variable speed 12volt winch that I put rope on to run the mill. both the chainsaws have remote throttles. I'm looking forward to milling this log! I have access to a gopro to mill the process.
any advice on thickness/drying of the slabs? I thought cutting them about 120 mm thick (5'') but I have no experience with drying/warping of slabs these size. I know beech does move a lot. I can bring the slabs to the lumber mill across to street, to have them dried, but i'm afraid they have very little to no experience drying this stuff. I'm thinking about buying a logosol sauno kiln, any experiences? would love to hear.
some more pictures of the log:
I have started a new project lately, I've bought a beech logs that measures 1.85 meter/ 73'' at the butt and is 5 meters long (196'') It weights 9.5 tons. I have been chainsaw milling since i was 18, so a couple of years of experience but this is my largest log so far. but i only cut maybe 2 logs a year because I don't really have the space to mill the logs. but gladly my employer let me delivery this log to my work so I can mill it there. this really helps because I can also use all the equipment; forklifts, woodworking/metalwork equipment.


stihl880 with 48'' for scale
I have a 42'' alaskan style mill but logosol/stihl (the red frame) with a 48'' bar and i have a logosol big mill basic system. But I have always been intrigued by the dual head milling setups. and since I usually cut slabs for table tabs etc. I have had a couple situations were I have been slabbing freehand because my other mill couldn't handle the logs.
so I've started making a new dual-headed mill. this will run a 87'' bar, with 404 stihl ripping chain. I've constructed the mill with aluminium profiles 40 x 80 mm, and made the rest out of metal. i've used the existing holes in the bar to mount the bar to the mill. I figured this was better than bar clamps since this would allow me to remove the chain for sharpening easiers. for this reason I also plan on running without clutch cover. only a clamp plate. I will add another safety guard so don't worry..
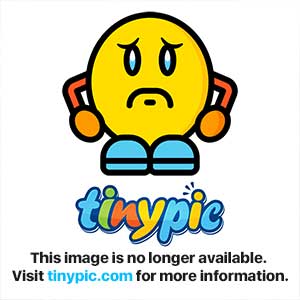
the big problem that occurs with these long bars is bar sag. I have fitted a couple plates to tension the bar, this seems to work, at first the bar had sagged quite a bit even with the 2 powerheads. but I was able to remove this sag with the adjustment bolts.
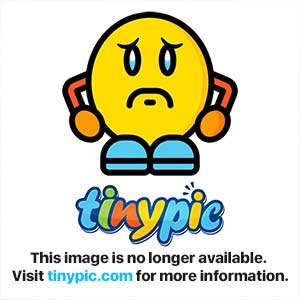
I plan on making 2 U-shaped guide shoes under the mill to run over rails. I have aluminium 100x100 rails to run over. I have a variable speed 12volt winch that I put rope on to run the mill. both the chainsaws have remote throttles. I'm looking forward to milling this log! I have access to a gopro to mill the process.
any advice on thickness/drying of the slabs? I thought cutting them about 120 mm thick (5'') but I have no experience with drying/warping of slabs these size. I know beech does move a lot. I can bring the slabs to the lumber mill across to street, to have them dried, but i'm afraid they have very little to no experience drying this stuff. I'm thinking about buying a logosol sauno kiln, any experiences? would love to hear.
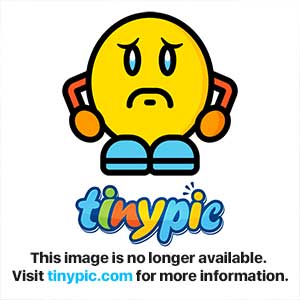
some more pictures of the log:
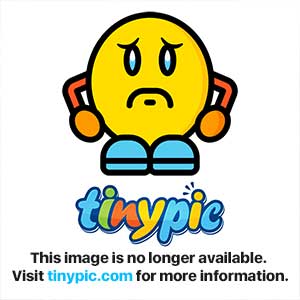