DaltonPaull
ArboristSite Operative
I just picked up a used ripsaw in good condition with an extra set of guide rails. I got it thinking that it would be great for cutting thin boards and quartersawing - basically the stuff that's too wasteful with the CSM. I've been cutting some western red cedar blow downs and a long dead larch - starting by cutting some cants with the CSM using the ripsaw rails - a huge upgrade! Then I started sawing boards with the ripsaw but my cuts keep coming out wavey - I've played with the blade tension and changed blades but it seams like maybe the cedar is building up on the blades and causing the poor cutting. The cut quality/speed really goes down quick after a blade change. Maybe the surface rust on the blades that came with the ripsaw causes the cedar to stick to the blade? Does anyone lubricate ripsaw blades? Do you think the build up would cause the blade to wander?
The only thing that seams to help is going really slow - like CSM speed and I think I should be able to do better than that in cedar. I'm pretty disappointed in the amount of wavy boards I've produced so far and looking forward to climbing the learning curve!
The only thing that seams to help is going really slow - like CSM speed and I think I should be able to do better than that in cedar. I'm pretty disappointed in the amount of wavy boards I've produced so far and looking forward to climbing the learning curve!

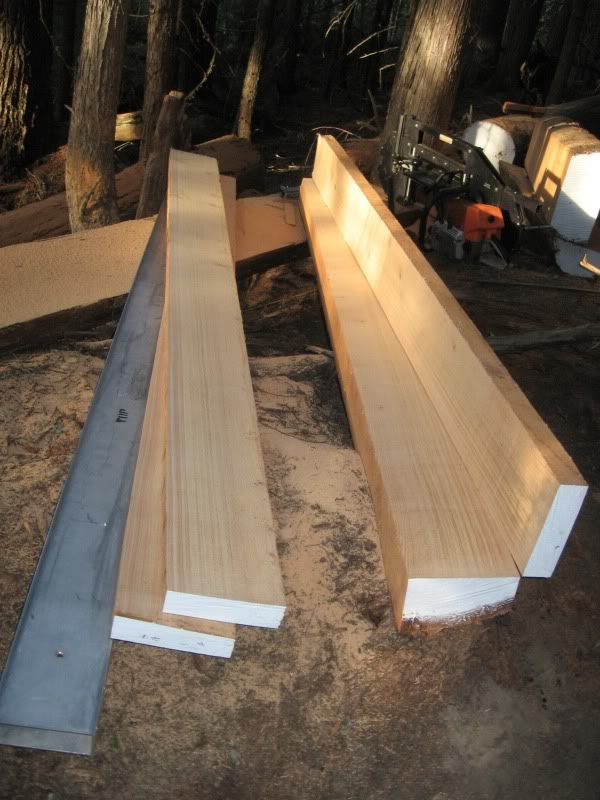
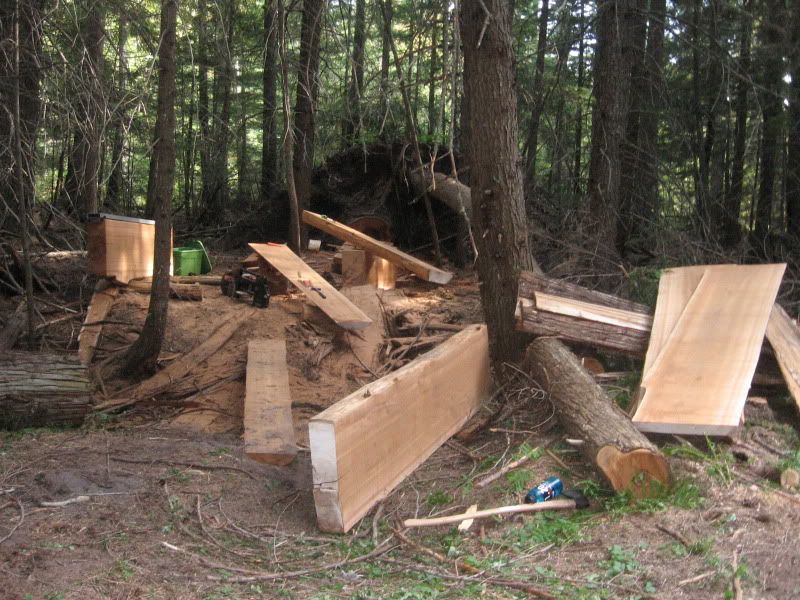