My 385XP has been leaking significant amounts of bar and chain oil. It also doesn't oil correctly - to the point where I am not running it because it is too hot.
Any suggestions to get this corrected will be appreciated.
I thought the problem may have been with adjustment screw on the bottom needed. It wouldn't tighten anymore (just turned) so I assumed it was in it's closed possition . I tried running the saw again, with no better results. Now the adjustment screw is missing - I will be replacing that.
Looking at the parts diagram, it shows a plug that looks to be at the end of the system -- I assume to slow the flow to the correct level??? Mine does not have that. Does yours? Not sure how it could have gone missing as I have not had the cover plate over that area off before. Is there supposed to be a plug there, or am I looking at the wrong place?
Pic shows parts diagram and photo of inside my saw. See green arrows for visualization of what I am talking about.
Thanks!
Any suggestions to get this corrected will be appreciated.
I thought the problem may have been with adjustment screw on the bottom needed. It wouldn't tighten anymore (just turned) so I assumed it was in it's closed possition . I tried running the saw again, with no better results. Now the adjustment screw is missing - I will be replacing that.
Looking at the parts diagram, it shows a plug that looks to be at the end of the system -- I assume to slow the flow to the correct level??? Mine does not have that. Does yours? Not sure how it could have gone missing as I have not had the cover plate over that area off before. Is there supposed to be a plug there, or am I looking at the wrong place?
Pic shows parts diagram and photo of inside my saw. See green arrows for visualization of what I am talking about.
Thanks!
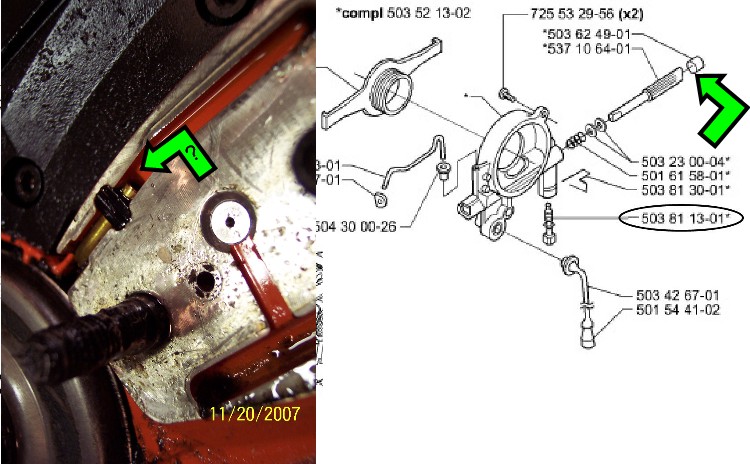