Greetings all! First time poster, but I have been creeping this forum as a technical resource for a few months. I am new to chainsaws and small engines in general. I wanted to share this rebuild project and sneak in a few questions 
My wifes sisters fiancé gave us a saw. It was in rough shape, basically like "I know you guys are in the bush 100+ days a year... you should have a power saw, here's one might last you a couple years... will get through firewood or get you our of a jam faster than that KB 650 pull saw".
I tried out it, cutting firewood and such. It was a pain to start and had obvious air leaks. You'd get through a cut and it would surge 4000-6000rpm off and on for about a minute before it would calm down. It also wouldn't start when hot, completely vapor locked. I started with the basic stuff. New fuel lines (pick-up line was leaking and return line looked like it was rotting) intake gasket. It cold started a little better, but that's about it.
Tried a cheap after market carb... not much different, then went down the carb turning rabbit hole (with the original carb) reading every article and watching every video I could find. Turned the L / H screws are the way in counted to note where they were initially set. It was something ridiculous like 4 & 1/2 turns. Set them both to 1 & 1/4 and started from there. Every time I thought I had it dialed in, I'd find it was still erratic after some use, or wouldn't cold start (like take your pick)
Reading into it more and watching vids, the main issue here (the surging) sure seems like an air leak. I pulled the muffler and noticed the piston was scoring a fair bit.
Still held decent compression, but at this point, figured maybe this saw can be a winter project... but now that I have caught the chainsaw bug, went out and bought a 445E II. Fired right up, runs great. Love it.
Well, this 445 II inspired me to get going on that 240, because I want that 240 to run like a new saw. I'm suspecting it just needs a gasket job between the crank case and cylinder, as well as a new tank vent and maybe check valve, but when I say NEW I mean NEW. Figured it's a free saw, and sure I could buy an equivalent saw for maybe $50-100 more than I am about to spend in parts, but I am going full saw nerd with this science experiment.
Parts ordered (all OEM): Piston/Cylinder kit, Crank Seal Bearing Assys, Carb, Clutch, Drum/Sprocket, tank vent, duck bill check valve, all new gaskets.
In addition to being slightly cheaper than buying a new equivalent saw, most parts I am taking out (like the clutch/sprocket, crank bearing seal assys) are still decent and will make fine spares. Even the old piston after some sanding and a new ring, along with the original cylinder (which looks great actually) could have a lot of life.
Waited forever and a day for the parts. Since HusqParts doesn't ship to Canada, had to go through a middle-man operation which costs some extra bucks and took 2 or 3 months to arrive. Finally parts arrived, so time to go to town on this!
[continued - need a break from typing and if you're still reading, probably need one too]
My wifes sisters fiancé gave us a saw. It was in rough shape, basically like "I know you guys are in the bush 100+ days a year... you should have a power saw, here's one might last you a couple years... will get through firewood or get you our of a jam faster than that KB 650 pull saw".
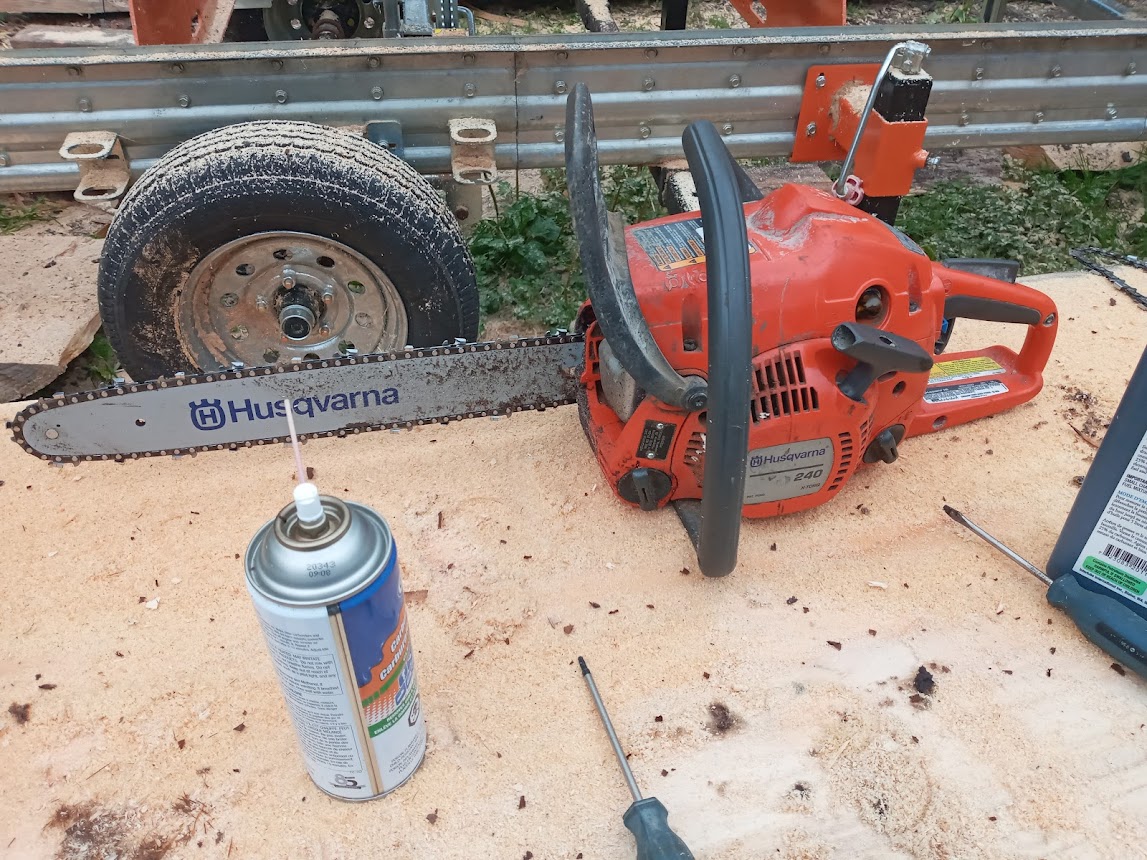
I tried out it, cutting firewood and such. It was a pain to start and had obvious air leaks. You'd get through a cut and it would surge 4000-6000rpm off and on for about a minute before it would calm down. It also wouldn't start when hot, completely vapor locked. I started with the basic stuff. New fuel lines (pick-up line was leaking and return line looked like it was rotting) intake gasket. It cold started a little better, but that's about it.
Tried a cheap after market carb... not much different, then went down the carb turning rabbit hole (with the original carb) reading every article and watching every video I could find. Turned the L / H screws are the way in counted to note where they were initially set. It was something ridiculous like 4 & 1/2 turns. Set them both to 1 & 1/4 and started from there. Every time I thought I had it dialed in, I'd find it was still erratic after some use, or wouldn't cold start (like take your pick)
Reading into it more and watching vids, the main issue here (the surging) sure seems like an air leak. I pulled the muffler and noticed the piston was scoring a fair bit.
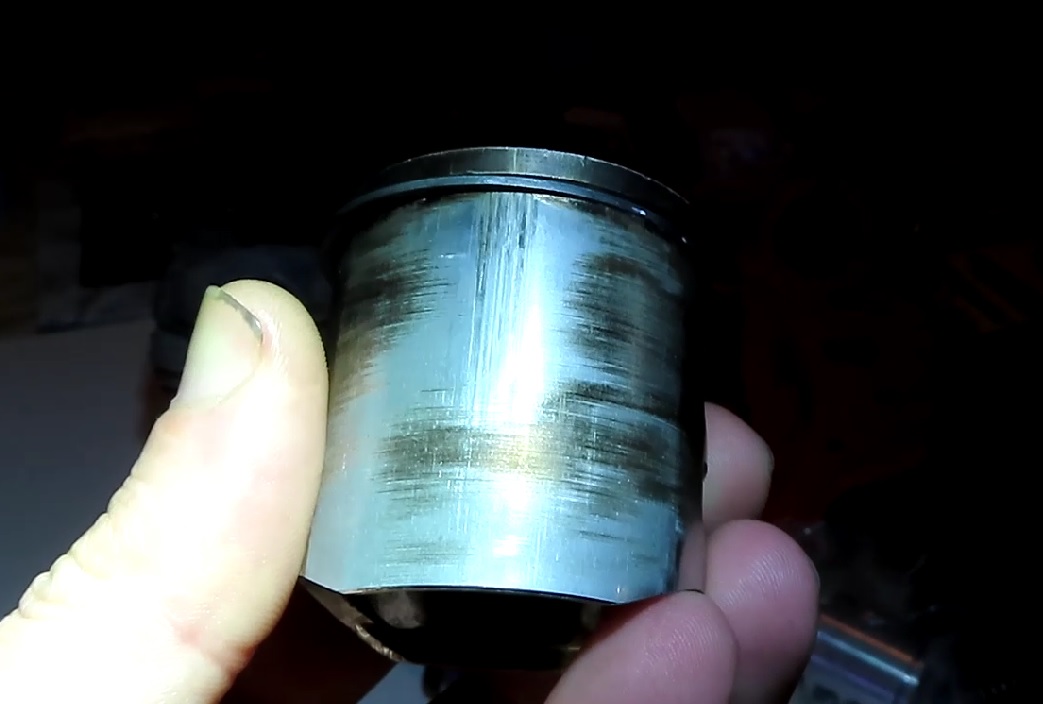
Still held decent compression, but at this point, figured maybe this saw can be a winter project... but now that I have caught the chainsaw bug, went out and bought a 445E II. Fired right up, runs great. Love it.
Well, this 445 II inspired me to get going on that 240, because I want that 240 to run like a new saw. I'm suspecting it just needs a gasket job between the crank case and cylinder, as well as a new tank vent and maybe check valve, but when I say NEW I mean NEW. Figured it's a free saw, and sure I could buy an equivalent saw for maybe $50-100 more than I am about to spend in parts, but I am going full saw nerd with this science experiment.
Parts ordered (all OEM): Piston/Cylinder kit, Crank Seal Bearing Assys, Carb, Clutch, Drum/Sprocket, tank vent, duck bill check valve, all new gaskets.
In addition to being slightly cheaper than buying a new equivalent saw, most parts I am taking out (like the clutch/sprocket, crank bearing seal assys) are still decent and will make fine spares. Even the old piston after some sanding and a new ring, along with the original cylinder (which looks great actually) could have a lot of life.
Waited forever and a day for the parts. Since HusqParts doesn't ship to Canada, had to go through a middle-man operation which costs some extra bucks and took 2 or 3 months to arrive. Finally parts arrived, so time to go to town on this!
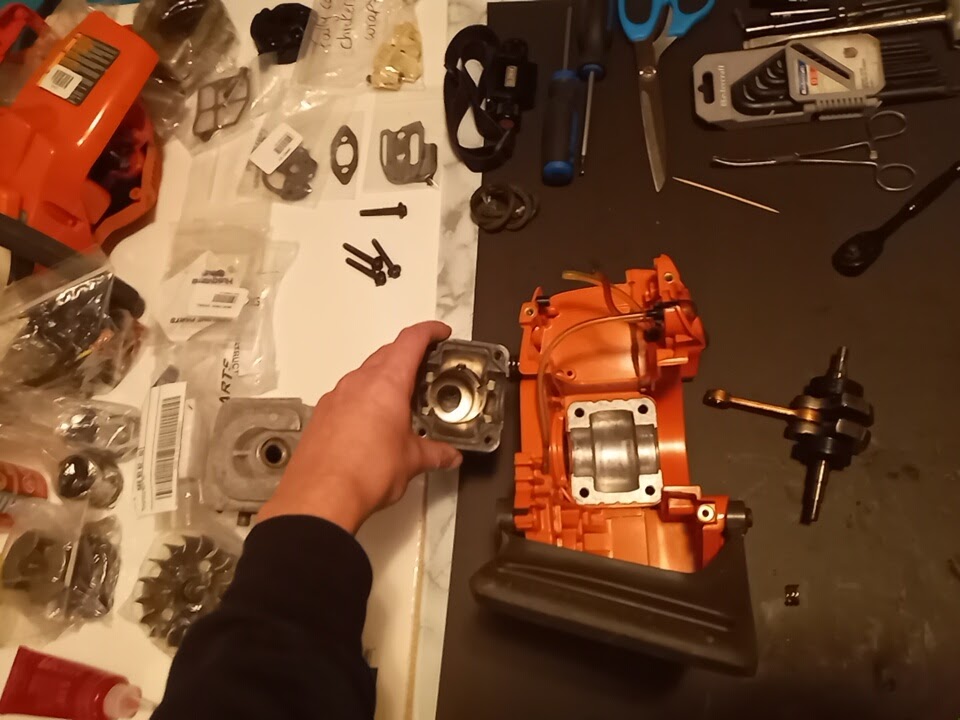
[continued - need a break from typing and if you're still reading, probably need one too]