Hi All,
This is my first post here but have been following the forum for quite a while especially this Huztl MS660 thread. I recently got one of these Farmertec ms660 kits and although this is my first time assembling a saw from scratch I have in the past had a number of other saws apart so thought I'd give it a go. Yesterday I got the crank case together (which was the bit that daunted me a bit but in the end turned out to me much much easier than I had expected). This morning I fitted the piston and cylinder and all seemed well but then ran across a problem whilst turning it over to check everything that has me totally confused....
With the base gasket in place and cylinder bolted down - turning the crank over by hand the saw will not reach anywhere close to TDC (or of course pass it) - the top of the piston is hitting the top of the cylinder / squish band as far as I can tell and stops with a definite metallic clunk. On releasing the cylinder bolts a little at a time (to figure out how thick a base gasket might be needed) I find that to get the saw to turn over I'd need a base gasket in excess of 5.3mm - which is clearly not right.
Here is a photo of the gap i have with the cylinder resting on the piston at TDC:
Has anyone come across this issue before and is it something I'm completely missing or is it a faulty cylinder?
Your thoughts would be appreciated...
Paul.
This is my first post here but have been following the forum for quite a while especially this Huztl MS660 thread. I recently got one of these Farmertec ms660 kits and although this is my first time assembling a saw from scratch I have in the past had a number of other saws apart so thought I'd give it a go. Yesterday I got the crank case together (which was the bit that daunted me a bit but in the end turned out to me much much easier than I had expected). This morning I fitted the piston and cylinder and all seemed well but then ran across a problem whilst turning it over to check everything that has me totally confused....
With the base gasket in place and cylinder bolted down - turning the crank over by hand the saw will not reach anywhere close to TDC (or of course pass it) - the top of the piston is hitting the top of the cylinder / squish band as far as I can tell and stops with a definite metallic clunk. On releasing the cylinder bolts a little at a time (to figure out how thick a base gasket might be needed) I find that to get the saw to turn over I'd need a base gasket in excess of 5.3mm - which is clearly not right.
Here is a photo of the gap i have with the cylinder resting on the piston at TDC:
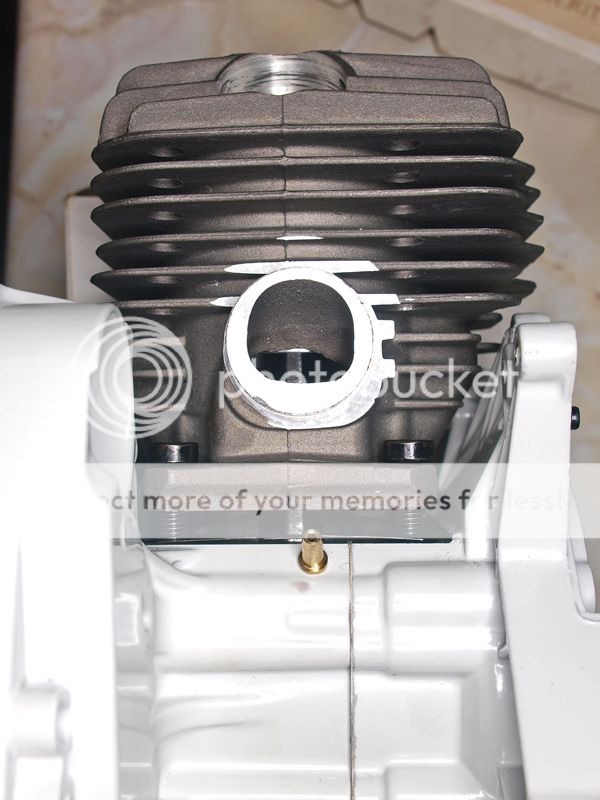
Has anyone come across this issue before and is it something I'm completely missing or is it a faulty cylinder?
Your thoughts would be appreciated...
Paul.