promac850
formerly promac610
Well, I pulled the compressor's head apart, and this is what the valve looks like...
I reckon that is going to either need some weld build up and regrind/remachine job or a replacement valve (good luck finding one, this thing is from around 1916) to make it service ready again... it's obvious this thing has been used, and a lot.
Towards the top of the stem, notice the threads that got stripped... apparently there used ot be a nut on there, but someone f'd it up, so they cut a little bit of the top of the stem off, and then drilled a hole for a little pin and put that in there, then staked the pin in spring retainer. It worked, only problem is that flipping that little compression release lever doesn't push down on the valve, since the stem is that much shorter.
Towards the bottom, you can see that the stem is very worn... it rocks a lot in the 'valve guide', which is really just the cast iron head itself... there is no bronze valve guide like on an automotive engine...
Any ideas?
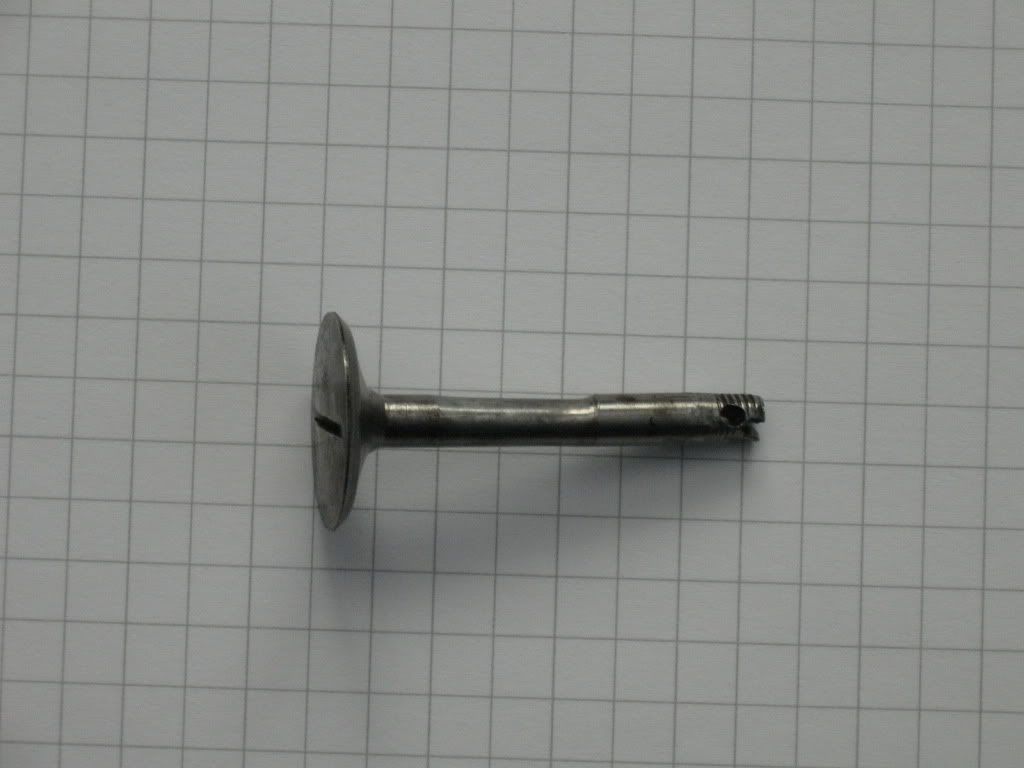
I reckon that is going to either need some weld build up and regrind/remachine job or a replacement valve (good luck finding one, this thing is from around 1916) to make it service ready again... it's obvious this thing has been used, and a lot.
Towards the top of the stem, notice the threads that got stripped... apparently there used ot be a nut on there, but someone f'd it up, so they cut a little bit of the top of the stem off, and then drilled a hole for a little pin and put that in there, then staked the pin in spring retainer. It worked, only problem is that flipping that little compression release lever doesn't push down on the valve, since the stem is that much shorter.
Towards the bottom, you can see that the stem is very worn... it rocks a lot in the 'valve guide', which is really just the cast iron head itself... there is no bronze valve guide like on an automotive engine...
Any ideas?
Last edited: