Jim Timber
1/4 bubble off
Messy as hell with metal chips everywhere? 
I didn't get the walking beams quite done, but I'm starting to hit the end of my day and I don't want to mess up what's coming next.
When I can, I cut a shoulder on axle stubs and use that to help align them. These are 1.25" seal surface 1" shanks so I just cut the back shoulder to 1" to make drilling the mounting holes easy. The surface finish doesn't matter inside the beam, so I hogged it with no regard for what a choppy mess it wound up with. Holes never drill to exact size either, so I cut the stubs once I knew the exact diameter they were going into. Makes for a nice snug fit.
I didn't get the walking beams quite done, but I'm starting to hit the end of my day and I don't want to mess up what's coming next.
When I can, I cut a shoulder on axle stubs and use that to help align them. These are 1.25" seal surface 1" shanks so I just cut the back shoulder to 1" to make drilling the mounting holes easy. The surface finish doesn't matter inside the beam, so I hogged it with no regard for what a choppy mess it wound up with. Holes never drill to exact size either, so I cut the stubs once I knew the exact diameter they were going into. Makes for a nice snug fit.
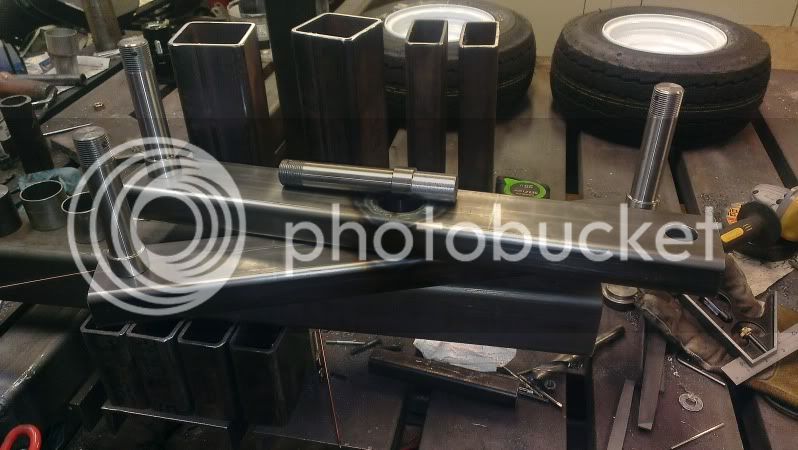