watsonr
Addicted to ArboristSite
- Joined
- Jan 3, 2010
- Messages
- 7,088
- Reaction score
- 2,130
Haven't seen any of these talked about here. A company sent me one for testing as an exclusive. Coating is really smooth, ports have a nice bevel on them. The saw is a tree service customer of mine that is always willing to provide test mules, gets free stuff, why not! Beat to death, top end smoked, filthy saw!
Clean saw, love that Purple Power... spray rinse and BAM, looks like new!
The cylinder, good pic to see the coating, port shape and bevel on the edges. I don't like the exhaust shape, flat roof... but I was told not to touch it! They are telling me that this is a 1 yr warranty against any failure... we'll see if it eats rings!:msp_sneaky: Nice clips, a little stiff like all the others, but no ears!
The finish is really nice but that exhaust roof. Piston had no casting flash left anywhere. The ceramic coating in this is exceptional, its the smoothest I've ever felt, combustion chamber is coated as well, wondering if the rings will actually seal. Project is waiting a fuel line, impulse tube and time to finish!
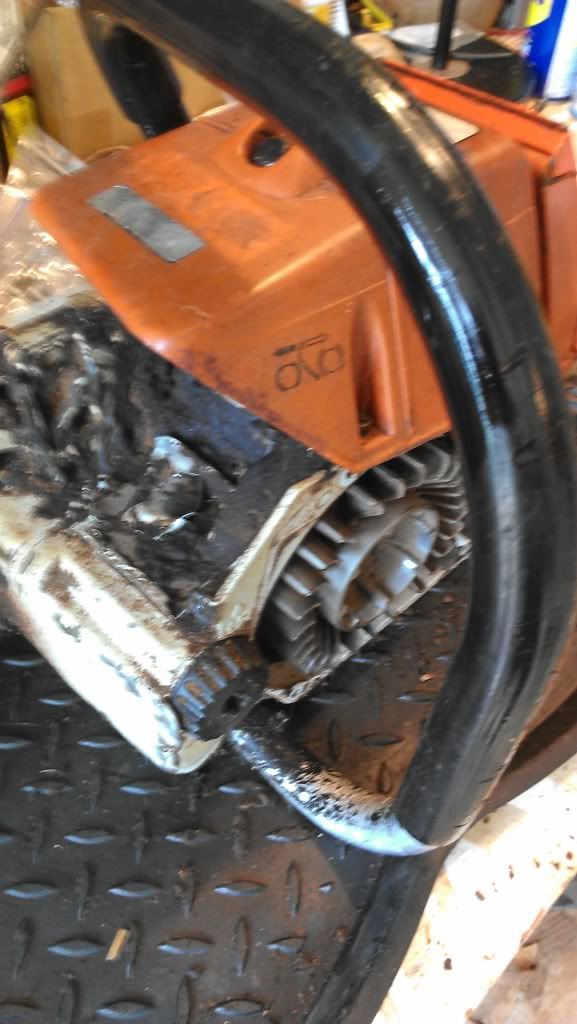
Clean saw, love that Purple Power... spray rinse and BAM, looks like new!

The cylinder, good pic to see the coating, port shape and bevel on the edges. I don't like the exhaust shape, flat roof... but I was told not to touch it! They are telling me that this is a 1 yr warranty against any failure... we'll see if it eats rings!:msp_sneaky: Nice clips, a little stiff like all the others, but no ears!
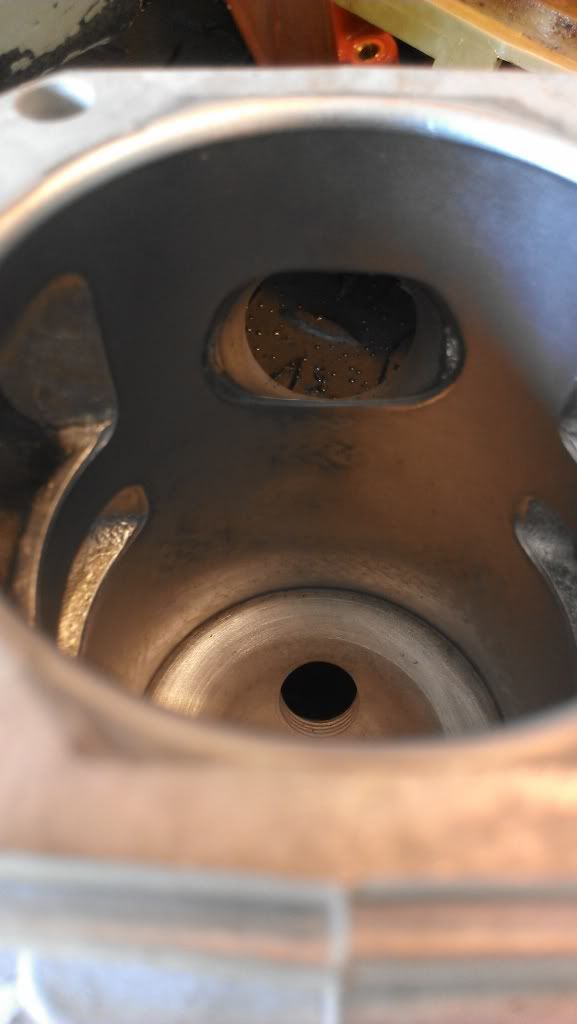
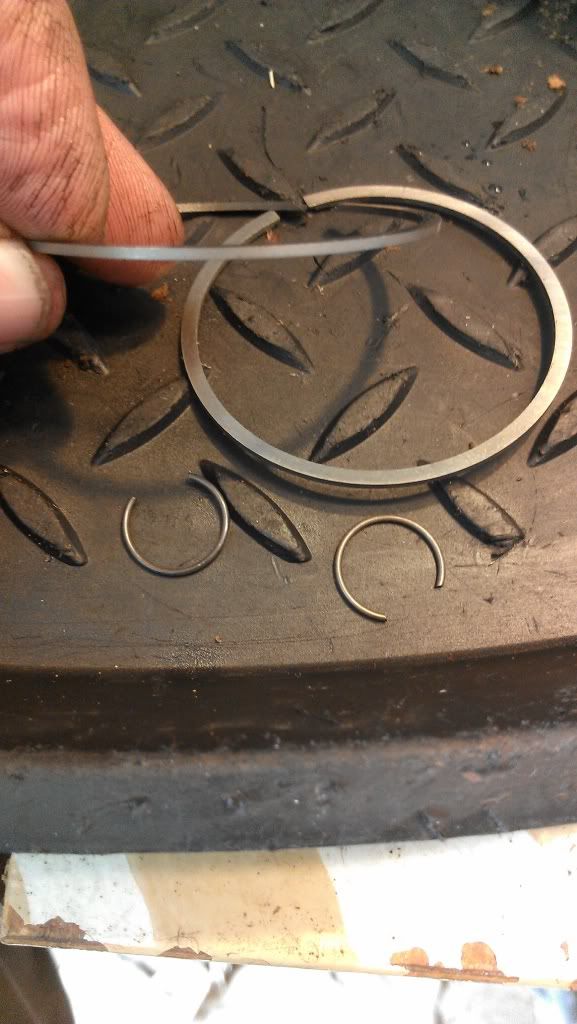
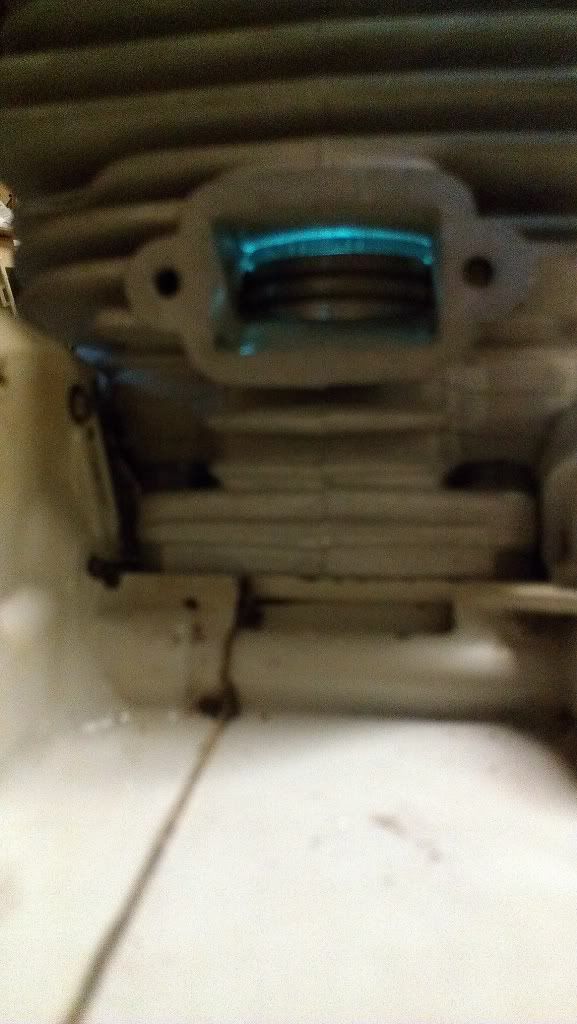
The finish is really nice but that exhaust roof. Piston had no casting flash left anywhere. The ceramic coating in this is exceptional, its the smoothest I've ever felt, combustion chamber is coated as well, wondering if the rings will actually seal. Project is waiting a fuel line, impulse tube and time to finish!
Last edited: