avarageerod
ArboristSite Lurker
I've gotten a lot of great ideas from this site, so I thought I would post up my OWB build.
So I acquired this old air compressor and thought it would be a good candidate for a OWB
First I needed to get it off my trailer since I used it often. I put it on this old farm trailer I have to keep it mobile and out of the garage while I worked on it.
Step one was to cut the end off
Since the trailer was kind of large to be in and out of the garage often and I found it hard to work on the trailer, I found a boat trailer for free and repurposed it. It doesn't look great, but it works.
I have a 60 gallon air compressor tank I'm going to use as a fire box. I am open for comments and suggestions since I really have no idea what I'm doing, I'm just guessing my way through this
So I acquired this old air compressor and thought it would be a good candidate for a OWB
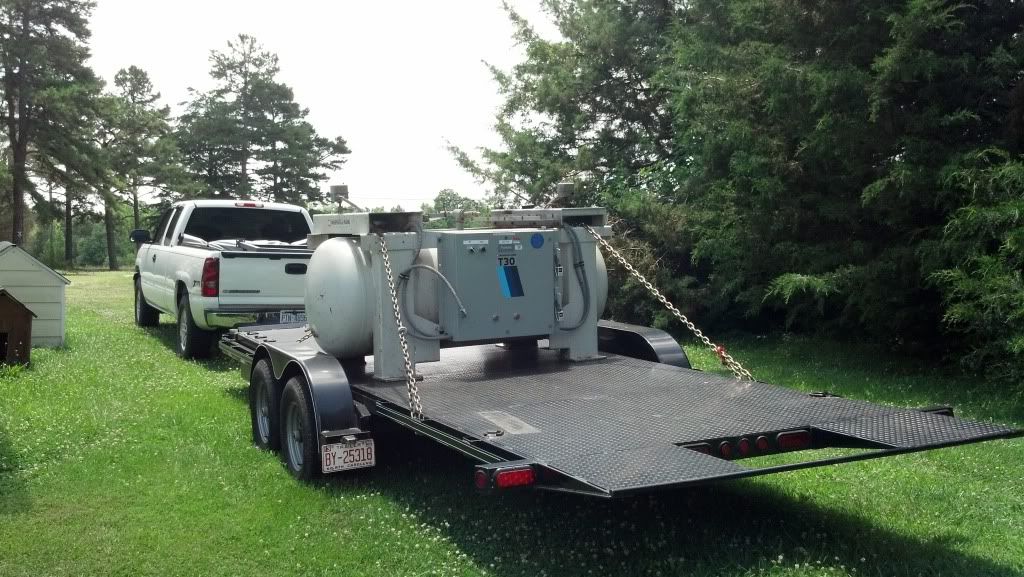
First I needed to get it off my trailer since I used it often. I put it on this old farm trailer I have to keep it mobile and out of the garage while I worked on it.
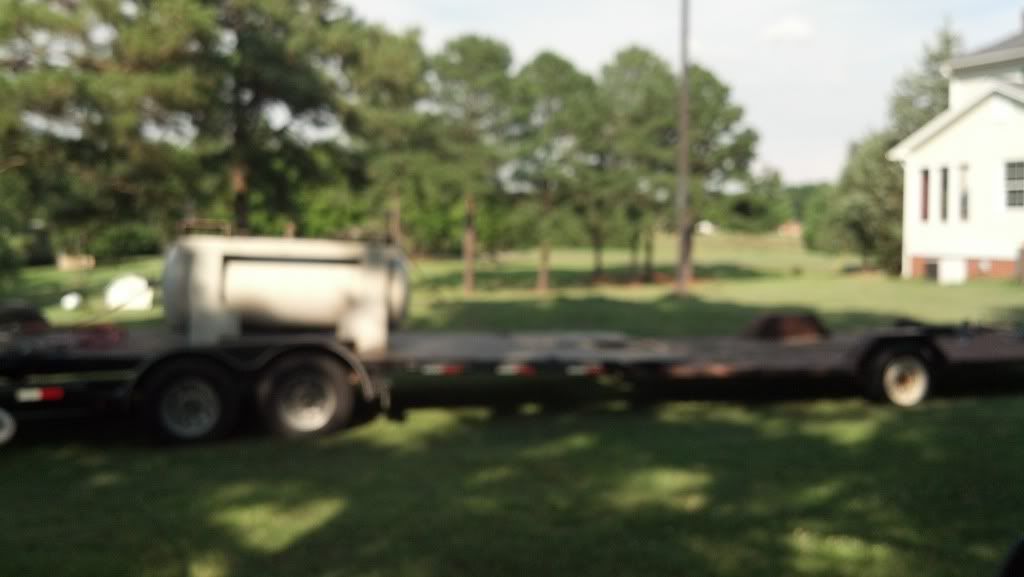
Step one was to cut the end off
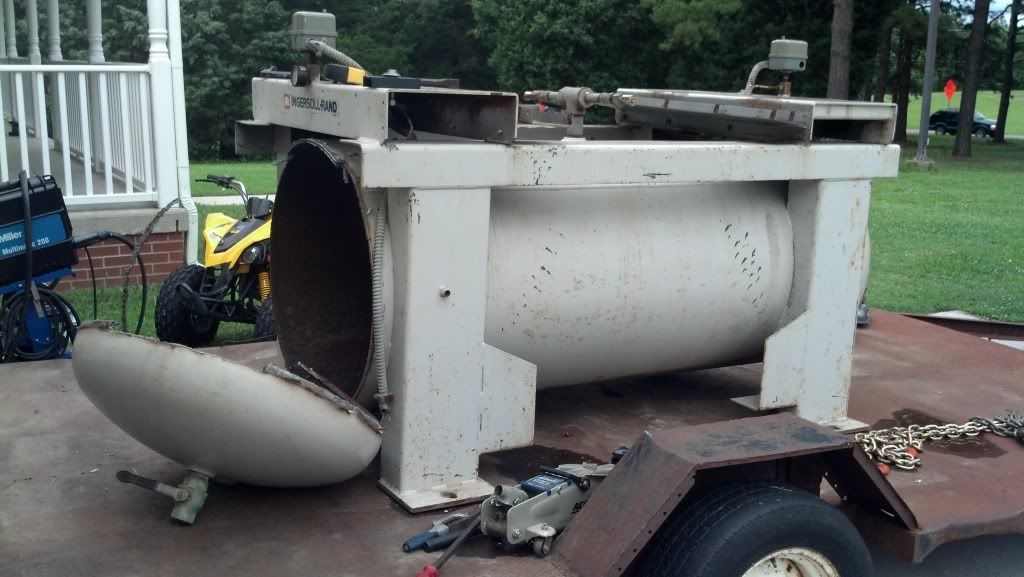
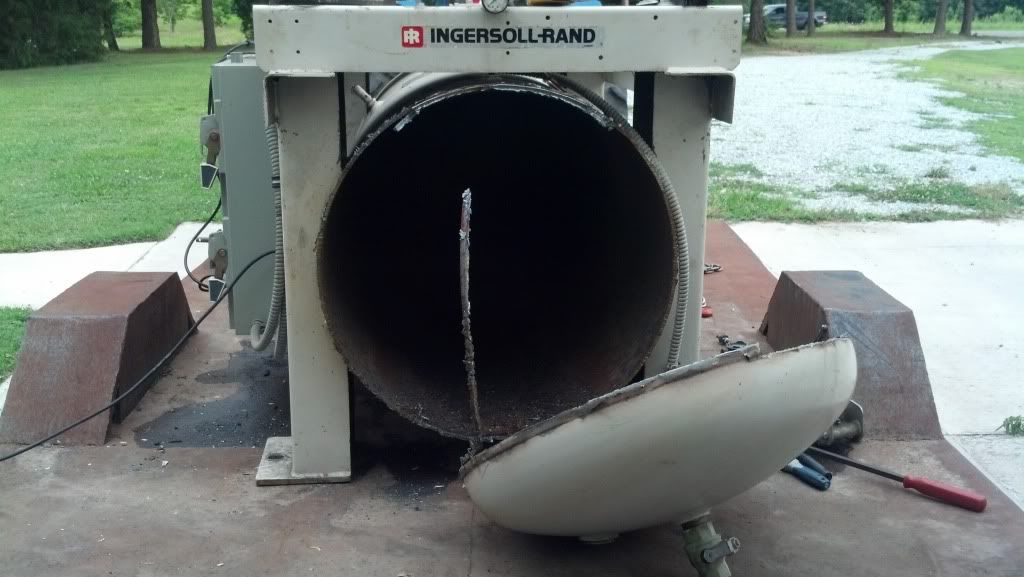
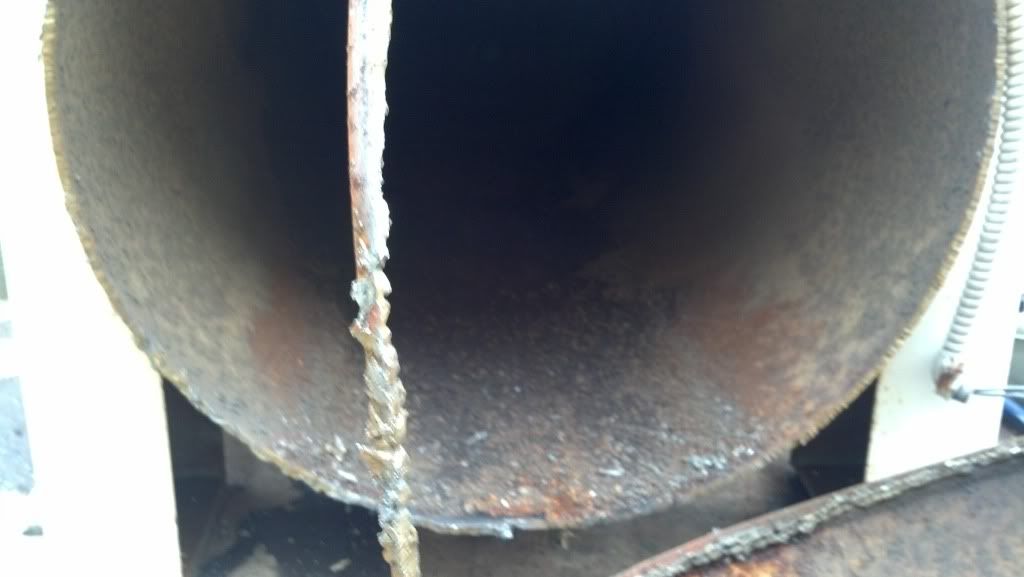
Since the trailer was kind of large to be in and out of the garage often and I found it hard to work on the trailer, I found a boat trailer for free and repurposed it. It doesn't look great, but it works.
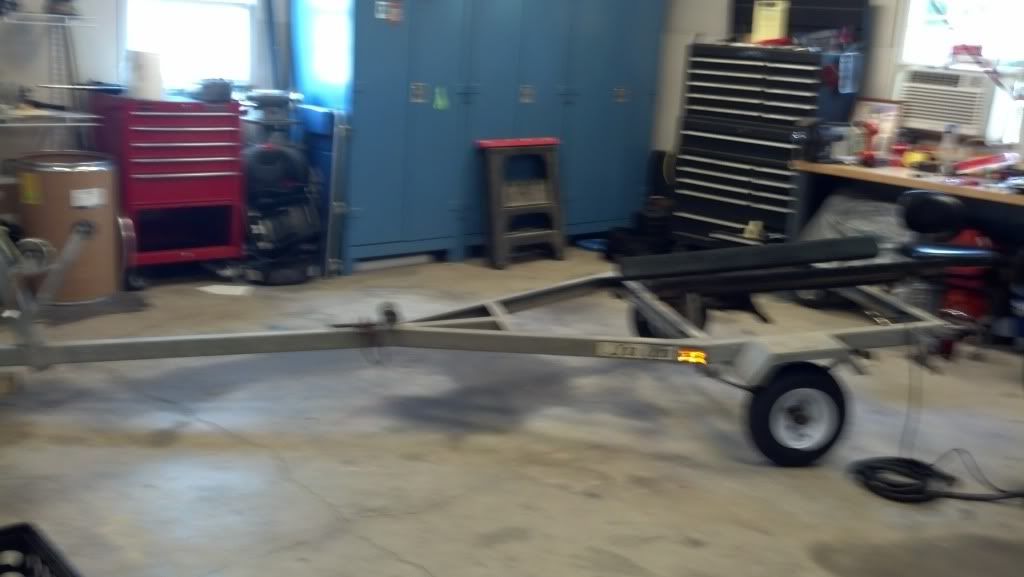
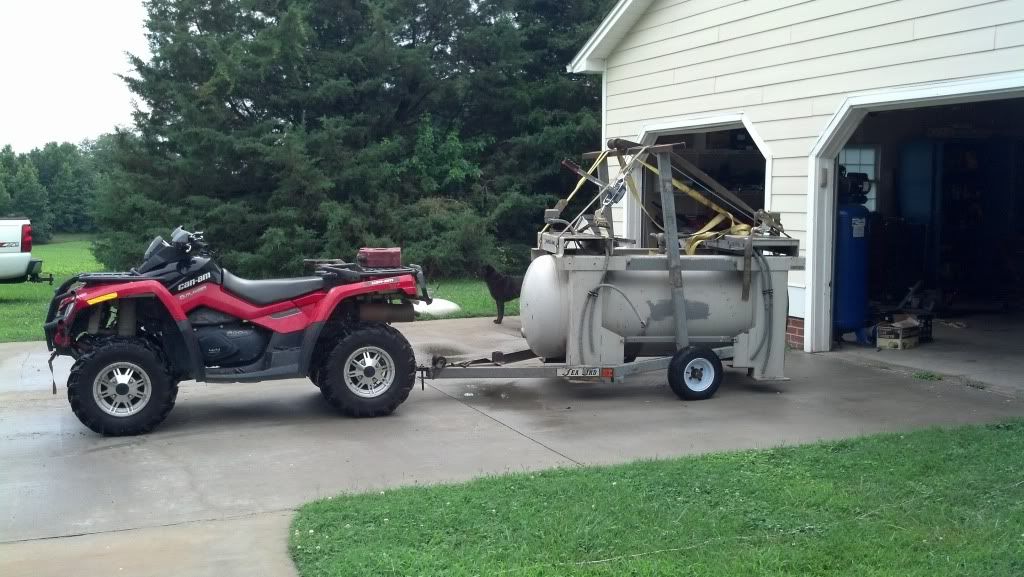
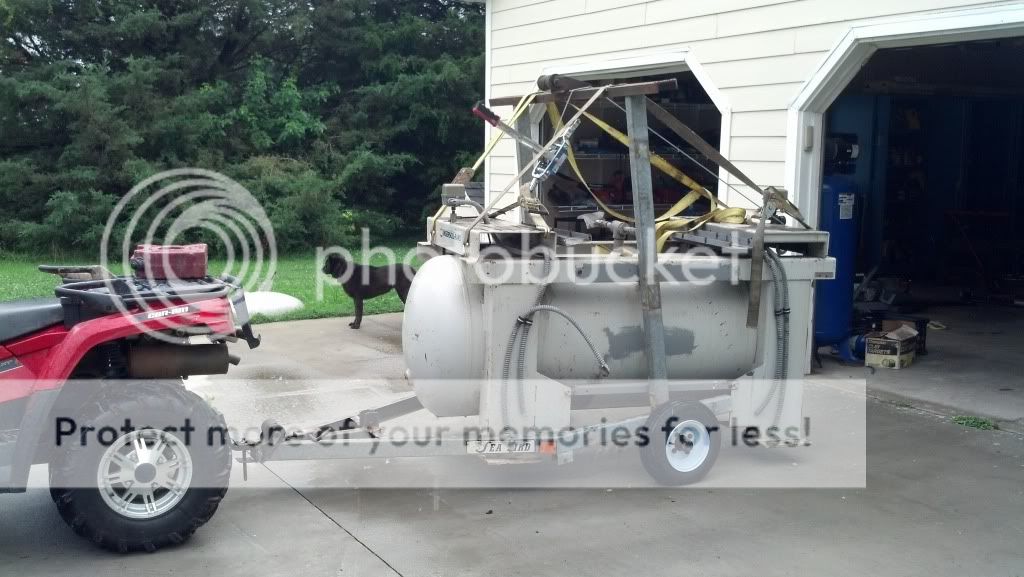
I have a 60 gallon air compressor tank I'm going to use as a fire box. I am open for comments and suggestions since I really have no idea what I'm doing, I'm just guessing my way through this