bnmc98
ArboristSite Guru
So, I have discovered a bad thing. My 288 has a hole in the decompression valve chamber that is giving me woes. (see image)
Looking for some advice. I tried a high temp thread sealer and it just turned it to ash. Was thinking of J B welding the plug into it and sealing it that way. But, I don't know if that will burn up too and cause a larger problem. Says its rated to 500 degrees.
Background:
- it does leak through the hole.
- This is supposedly a newer rebuild, my guess is that it is an aftermarket jug because it looks like a casting flaw to me.
- its a work saw so I don't care how it looks, I just need it to seal.
- cheap is good, don't really want to put a jug on it.
I am concerned because it looks like there is not a factory replacement avail for this saw, and I don't know what piston is in it so I don't know if I want to put a new jug on it. ( don't know if that would cause compatibility problems)
any advice would be great
Brian
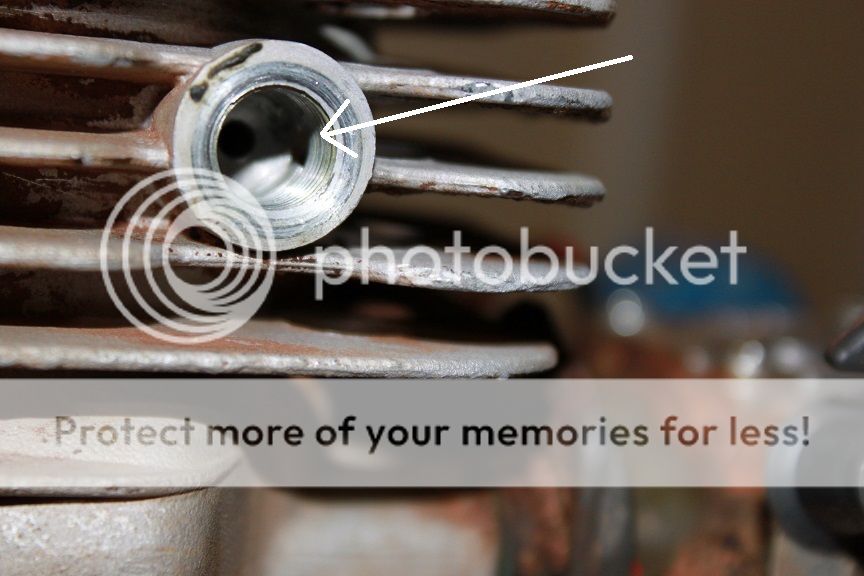
Looking for some advice. I tried a high temp thread sealer and it just turned it to ash. Was thinking of J B welding the plug into it and sealing it that way. But, I don't know if that will burn up too and cause a larger problem. Says its rated to 500 degrees.
Background:
- it does leak through the hole.
- This is supposedly a newer rebuild, my guess is that it is an aftermarket jug because it looks like a casting flaw to me.
- its a work saw so I don't care how it looks, I just need it to seal.
- cheap is good, don't really want to put a jug on it.
I am concerned because it looks like there is not a factory replacement avail for this saw, and I don't know what piston is in it so I don't know if I want to put a new jug on it. ( don't know if that would cause compatibility problems)
any advice would be great
Brian