built this over the past few days (hour here, hour there) in hopes of milling our own wood to build a sugar shack for our maple syrup operations....
interested in anyone's opinion on it, and what should be improved or added onto it. i have never built one, or even used on for that matter. the saw is my husky 372 xp, which i plan (or hope) to use to mill...
thanks!!
interested in anyone's opinion on it, and what should be improved or added onto it. i have never built one, or even used on for that matter. the saw is my husky 372 xp, which i plan (or hope) to use to mill...

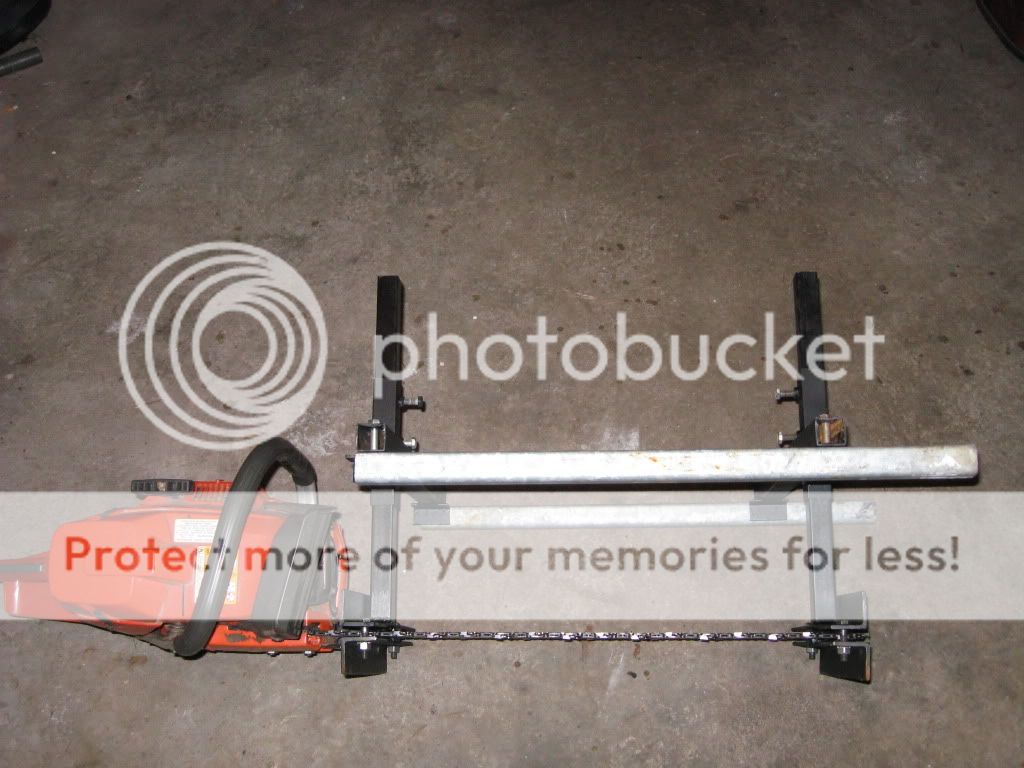
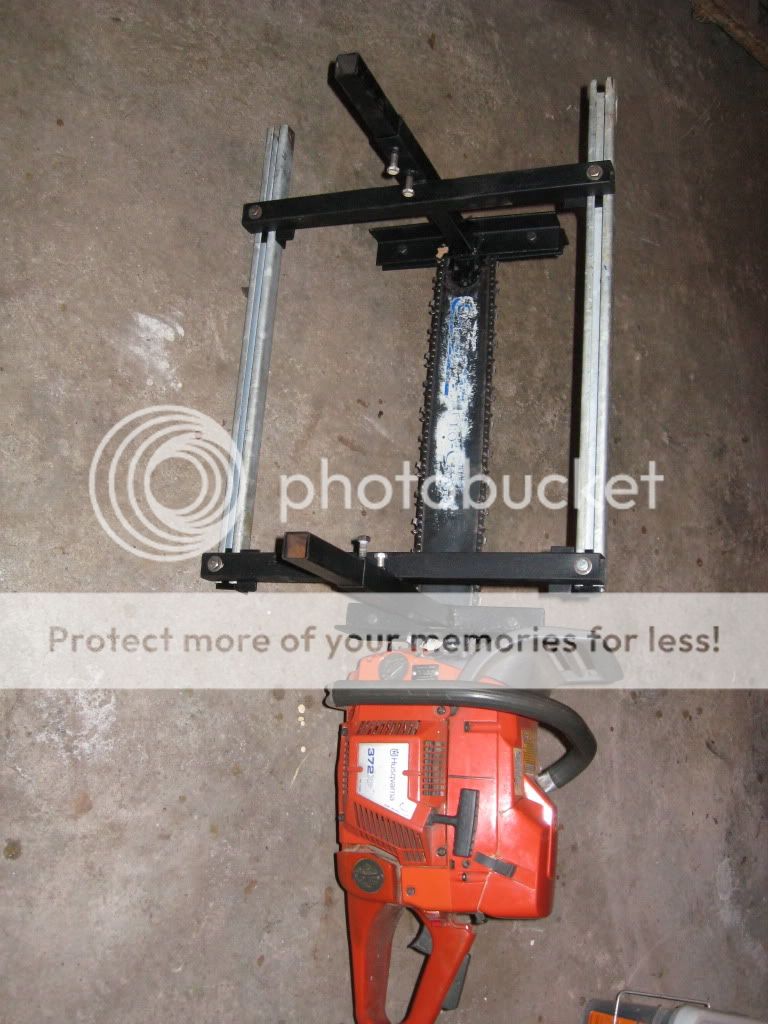
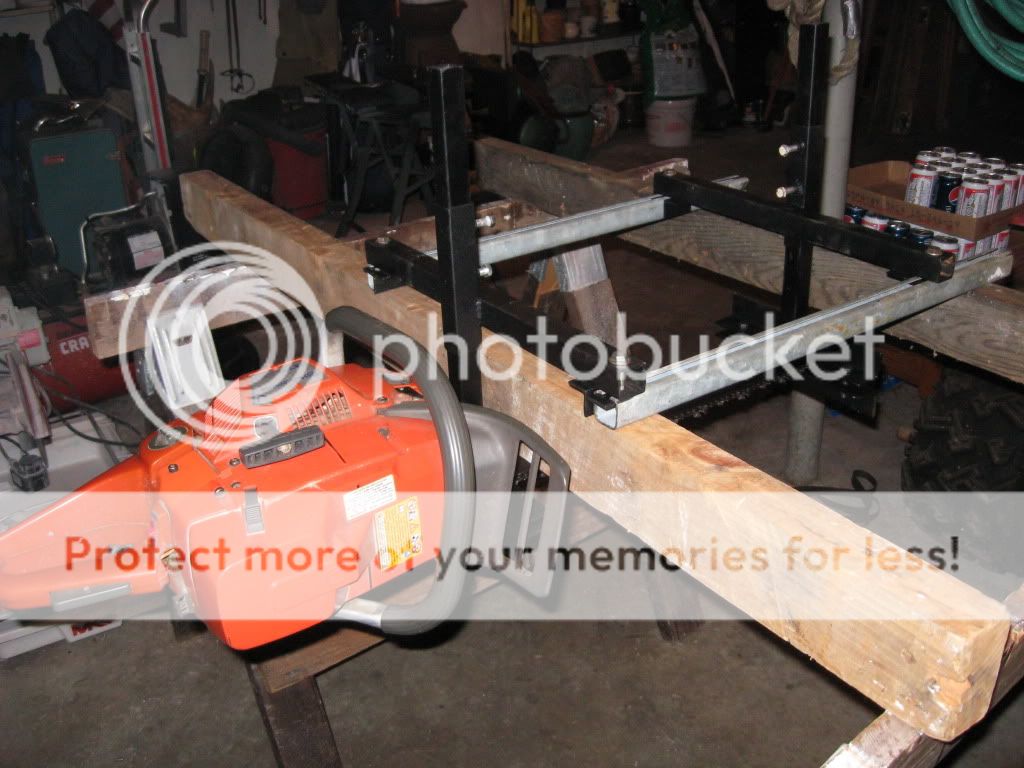
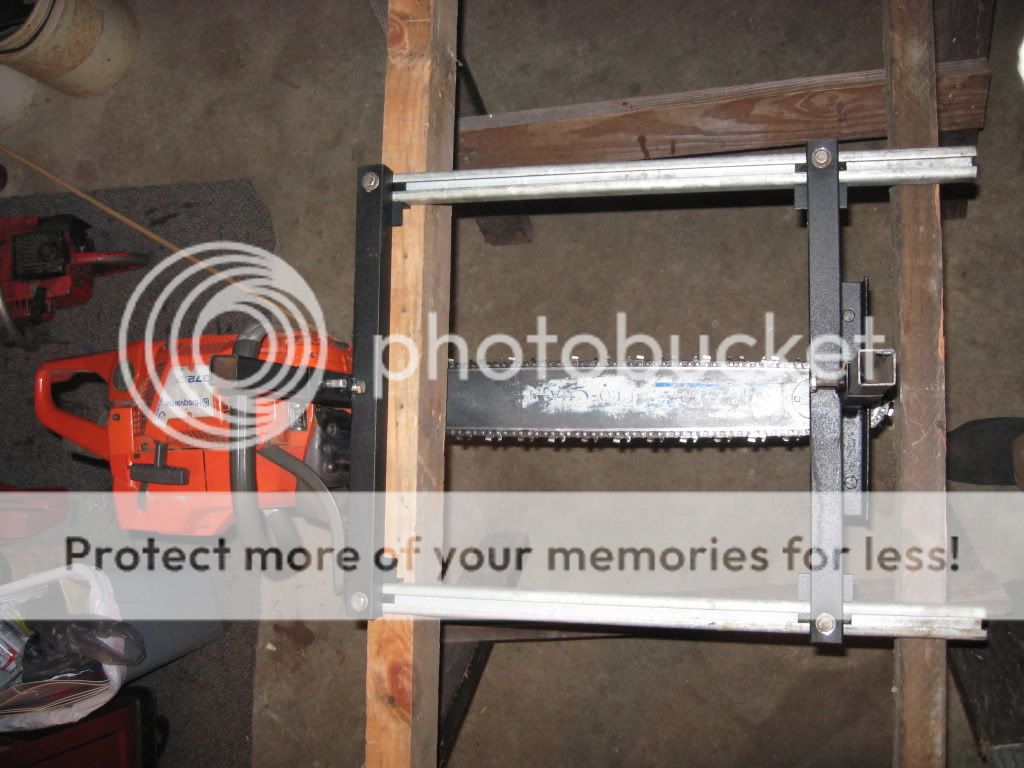