Definitive Dave
wanna-be saw racer, saw hoarder, parts whore
- Joined
- Jul 27, 2013
- Messages
- 2,118
- Reaction score
- 5,086
finished tearing down the 12mm 044 that is going to be the donor saw for Al's uber-head 
this is what I found on the lower felling spike mounting hole, it protrudes just a little, no way I could grab it with any tool I have or know of
I am guessing that drilling and then using an easy out screw extractor is the way to go.
I have plenty of good quality bits small enough but the piece is awkward and I am pretty sure it will be hard to drill right with a tiny bit in my BS little crapsman benchtop drill press. And I have no extractor small enough.
I will probably take it to a local machine shop unless somebody has another better idea.
I don't want to make it an oversized thread if at avoidable.
otherwise looks to be an easy swap, good bearings and seals, just a little cleaning



Dave
this is what I found on the lower felling spike mounting hole, it protrudes just a little, no way I could grab it with any tool I have or know of
I am guessing that drilling and then using an easy out screw extractor is the way to go.
I have plenty of good quality bits small enough but the piece is awkward and I am pretty sure it will be hard to drill right with a tiny bit in my BS little crapsman benchtop drill press. And I have no extractor small enough.
I will probably take it to a local machine shop unless somebody has another better idea.
I don't want to make it an oversized thread if at avoidable.
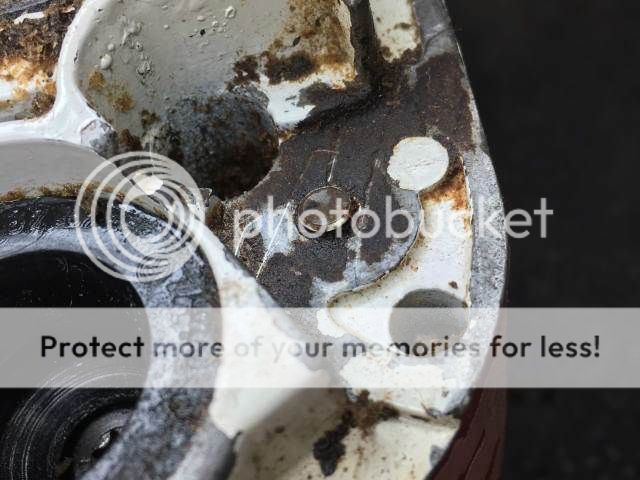
otherwise looks to be an easy swap, good bearings and seals, just a little cleaning
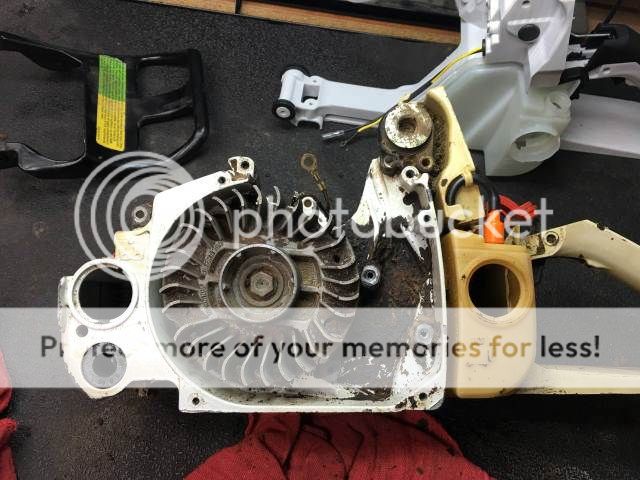
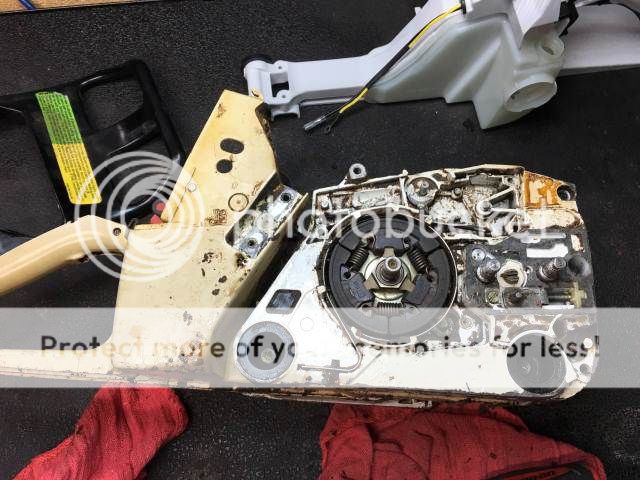
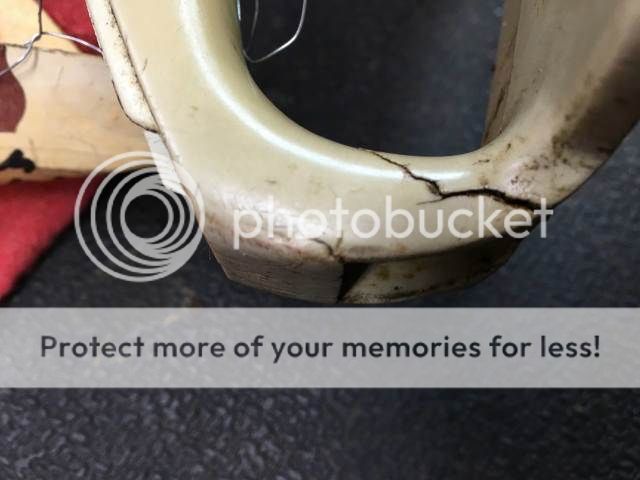
Dave