woodshop
Addicted to ArboristSite
For those that asked, here are details of the small horses I use when milling. Extra hassle getting the logs/cants up onto them, but when I do it sure saves the back and knees.
24" long
18 1/2" high
22" wide at base looking from end
legs are full 2" by 3" white pine
main beam across is solid 5" by 3" doug fir
end braces are 3/4 birch plywood (the good stuff, no voids)
side braces across legs are 3/4 x 4 1/2" white pine
aluminum indexed strip on top is 1/4" thick x 2" wide.
everything is glued and screwed, with quick and dirty coat of varnish to shed rain/oil
chocks are solid chunks of sweetgum 2 1/4 thick, 3" wide and 4 1/4" long with 1" angle iron one end that contacts log, with 1/4" metal pins on bottom where they fit into the aluminum strip.
Before I screwed on the aluminum strip, I dado-ed out an area so sawdust can accumulate, and every once in a while I just run something down them to clean out.
My goal was sturdy enough for a 24" 8ft long hardwood log, but light enough to throw in truck. As you can see in the pics where I cut into one end, using a long bar to trim up sides of log can be hazardous to the health of the horses.
24" long
18 1/2" high
22" wide at base looking from end
legs are full 2" by 3" white pine
main beam across is solid 5" by 3" doug fir
end braces are 3/4 birch plywood (the good stuff, no voids)
side braces across legs are 3/4 x 4 1/2" white pine
aluminum indexed strip on top is 1/4" thick x 2" wide.
everything is glued and screwed, with quick and dirty coat of varnish to shed rain/oil
chocks are solid chunks of sweetgum 2 1/4 thick, 3" wide and 4 1/4" long with 1" angle iron one end that contacts log, with 1/4" metal pins on bottom where they fit into the aluminum strip.
Before I screwed on the aluminum strip, I dado-ed out an area so sawdust can accumulate, and every once in a while I just run something down them to clean out.
My goal was sturdy enough for a 24" 8ft long hardwood log, but light enough to throw in truck. As you can see in the pics where I cut into one end, using a long bar to trim up sides of log can be hazardous to the health of the horses.
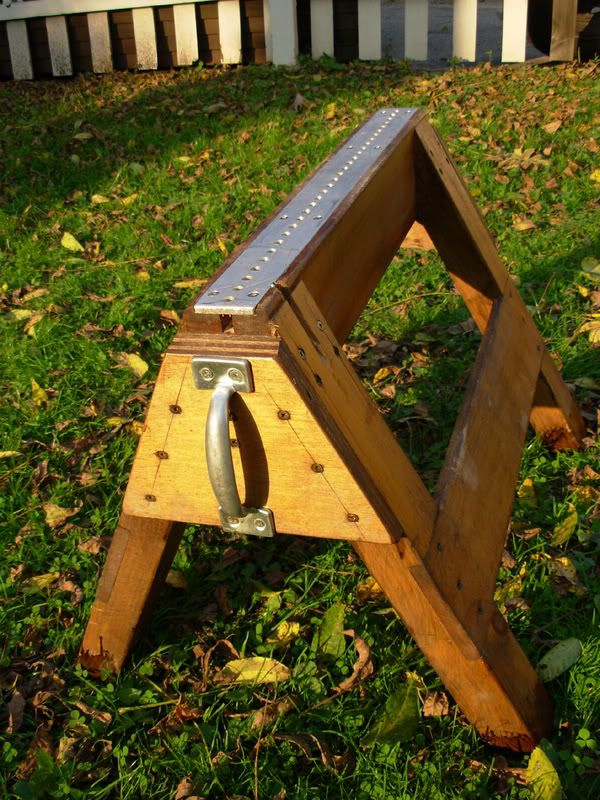
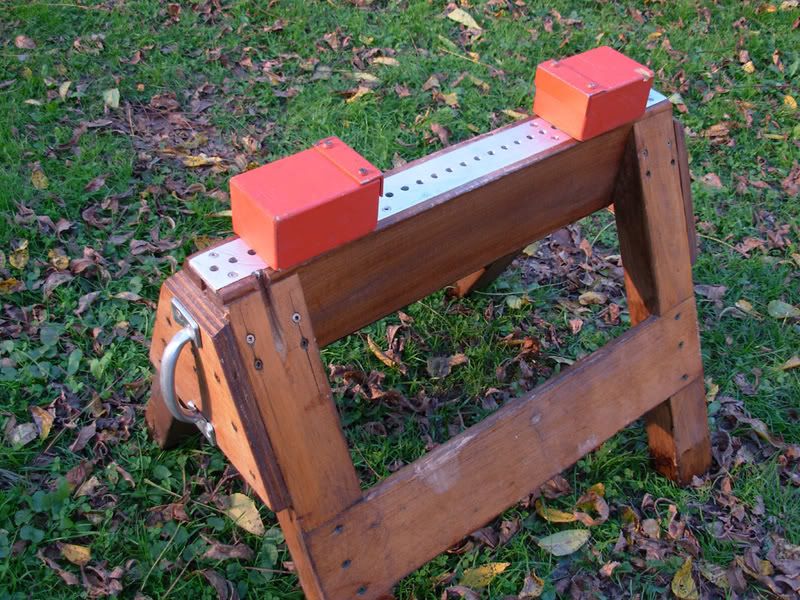
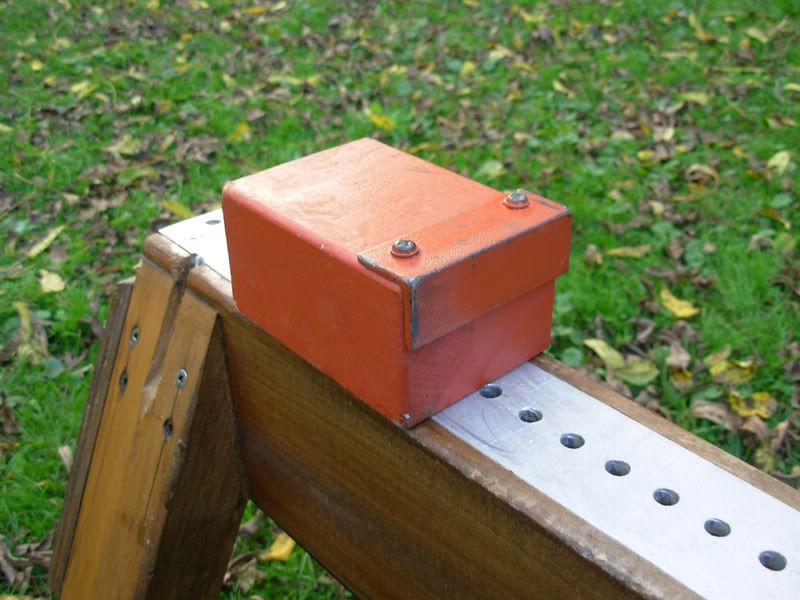
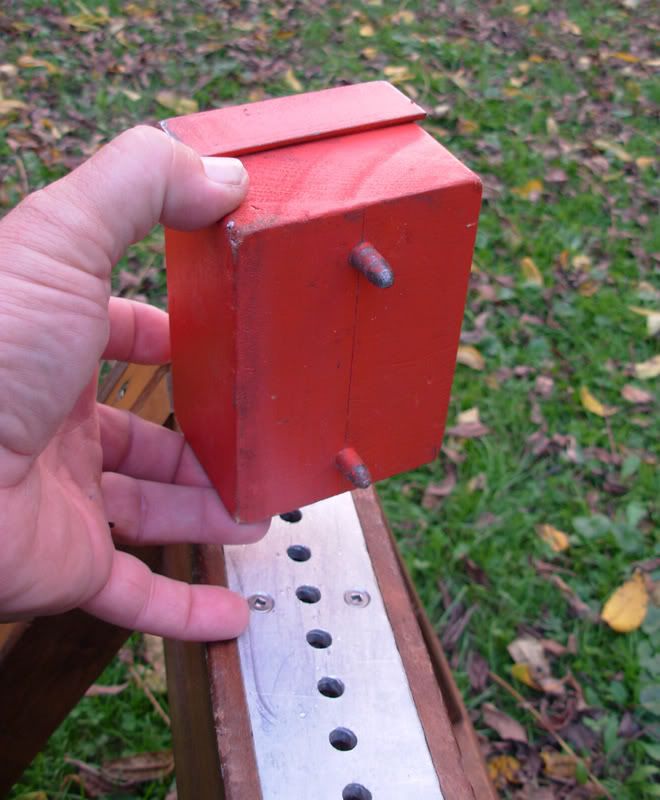
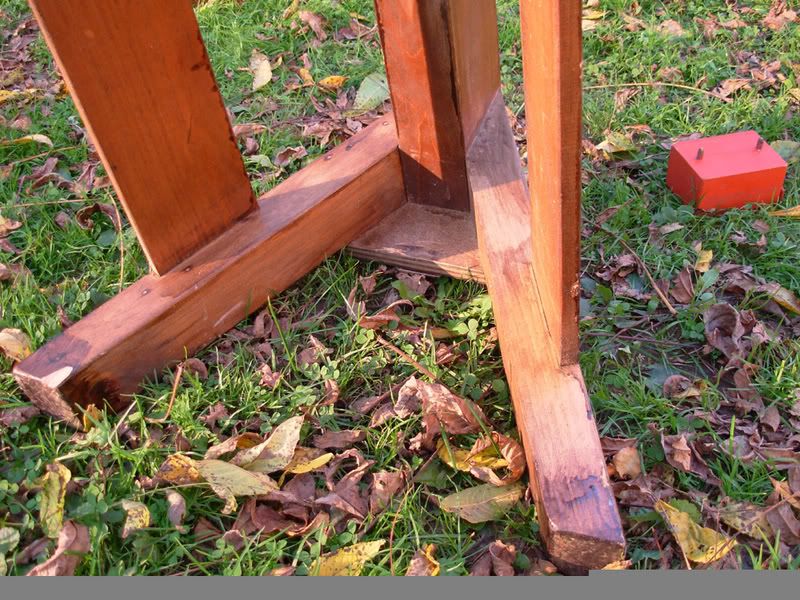
Last edited: