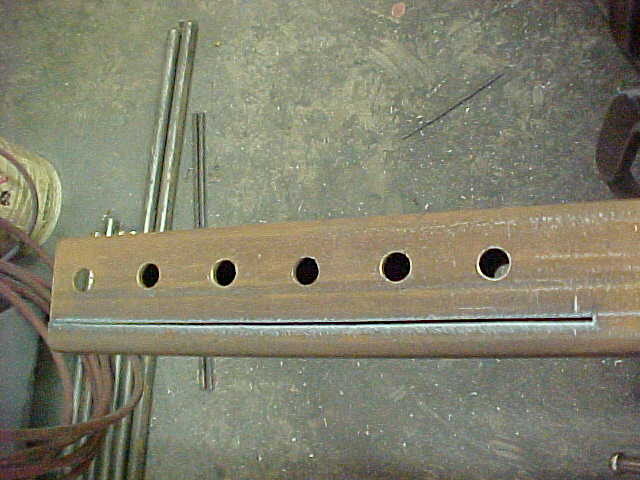
Once they were all drilled, I used the plasma torch to rough cut to length. I'm going to round the open end so leaving it long. Just quicker to cut this way and less wear on the chop saw blade.
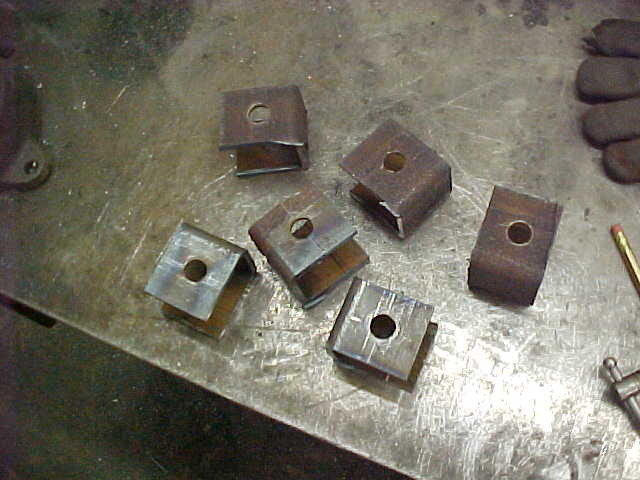
All cut up and ready to round the open end. I'll cut a short piece of round stock, center drill a 5/8" hole and bolt it to the bracket. I'll blend it out using the method shown before. Takes a little time but gives it a nice finish touch.
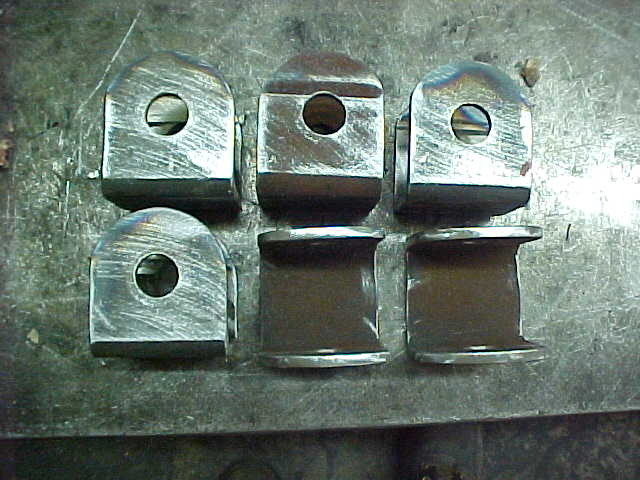
Got those all done and cleaned up. I'll work on the arms next. I have to make up some solid pivots for the ends that will be welded into the box tubing and will keep the wear to a minimum.
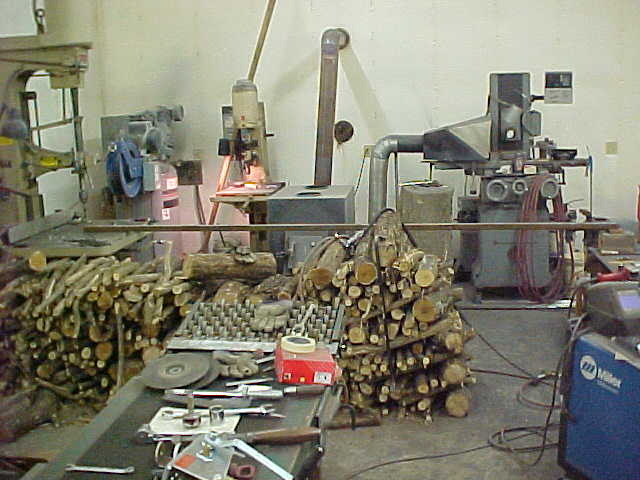
Marked the hole for the pivot and drilled it out. I'm drilling into a long bar and want them straight so I supported the far end and brought it to level with the table. Keeps everything straight that way. You can see I'm getting rid of the honeysuckle in here! Doesn't take but a few pieces to keep the shop nice.
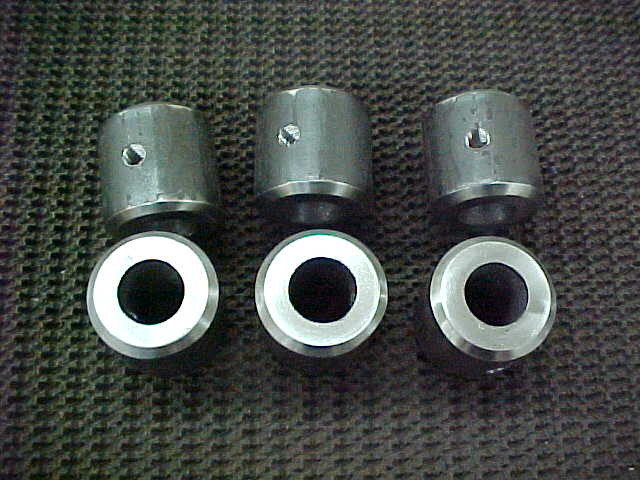
These are the bushings I'll weld into the ends of the box tubing. Made them out of bar stock. I chamfered the ends so when I grind them flush there is still weld there.Also drilled/tapped them all for zerks.
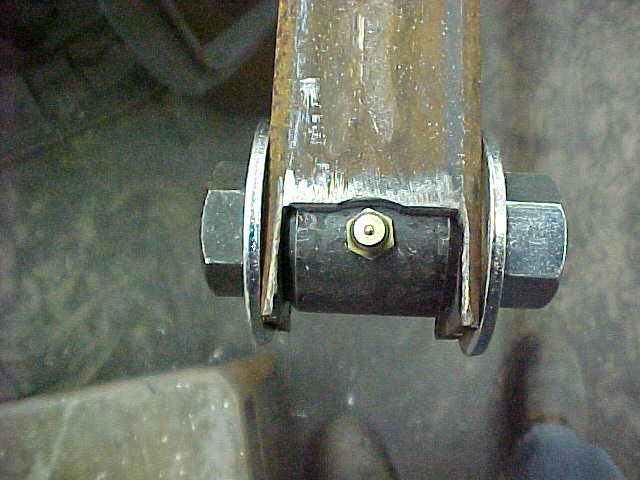
Recessed the tubing and held it all in place with a 5/8" bolt for welding. this way everything stays true and tight. I'll grind away the excess.
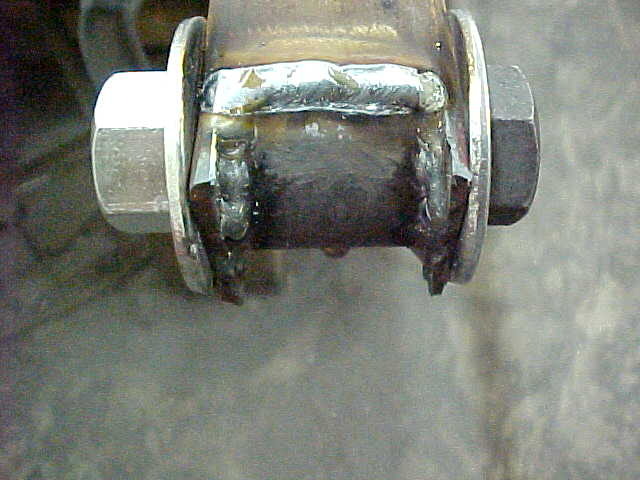
Quick welding here and it really is overkill but I want them solid.
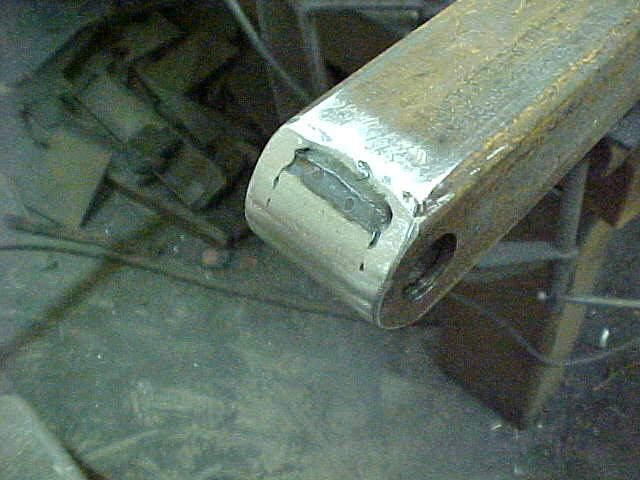
All blended out and ready to go. This way everything clears the mounts when it swings and just plain looks better.
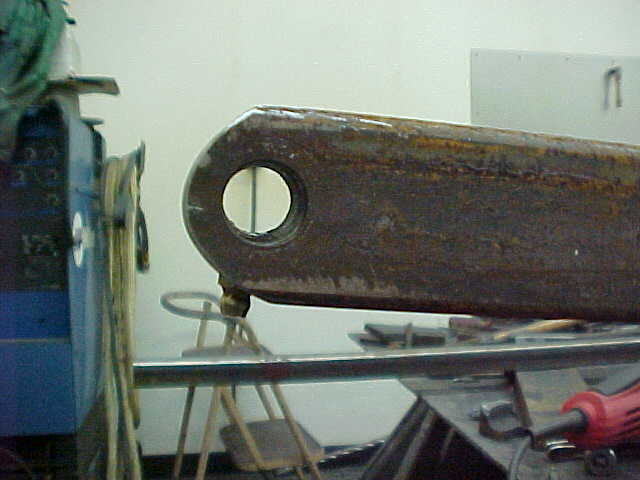
Here you can see the full radius and how it will be able to pivot.