This is the making of the Fixture to grind Depth Gauge or Rakers on chainsaw chain to equal depths and easier. I've done it by hand for years bur wanted something that would make this job easier and better at the same time. I have a surface grinder here at home and will use that as the way to grind. the fixture will just hold the chain and be adjustable for any chain out there.
Went to the metal piles and grabbed some stock. I'll use stainless on the guides and pins and mild steel for the base. That way it'll be magnetic when put on the surface grinder chuck and will hold.
Here's my surface grinder. I put a digital readout on it so I can repeat easily and redress, going back to the exact spot. You can do it without, which I have, but this makes it a lot easier
To hold the chain in place I'm planning on a snap clamp. They are adjustable and hold really well.
Here's a VERY rough sketch of what's in my head so you have an idea of where I'm trying to go with this
I cut 4 pieces for the chain holder and want to round the ends like a saw bar so the chain doesn't catch. Cut them the same and marked the ends. I threw in on the surface grinder to cut 45 degrees of the excess stock off.
You can get real close and make straight cuts with these.
This makes short work for rounding if you don't have a mill like me.
Marked a center hole and I'll do this on both ends. This will hold the together, evenly while I work them up.
Center drilled and drilled all the holes.
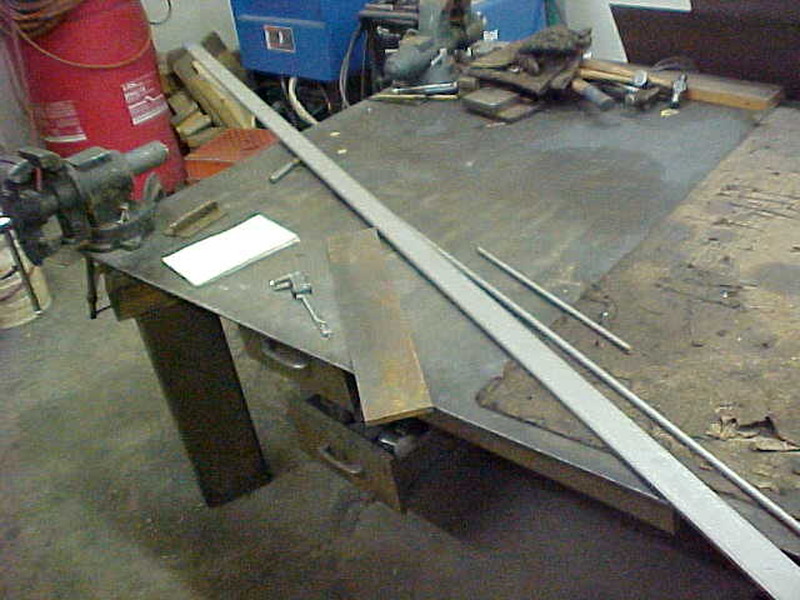
Went to the metal piles and grabbed some stock. I'll use stainless on the guides and pins and mild steel for the base. That way it'll be magnetic when put on the surface grinder chuck and will hold.
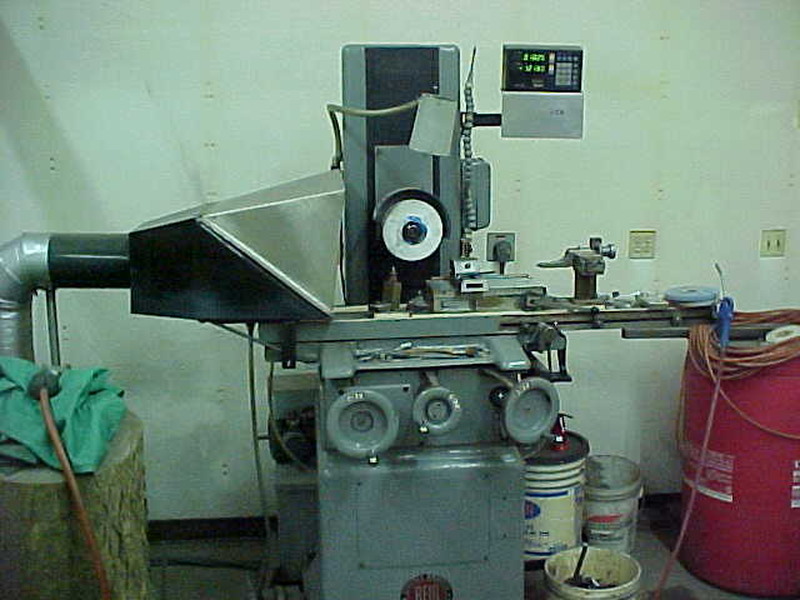
Here's my surface grinder. I put a digital readout on it so I can repeat easily and redress, going back to the exact spot. You can do it without, which I have, but this makes it a lot easier
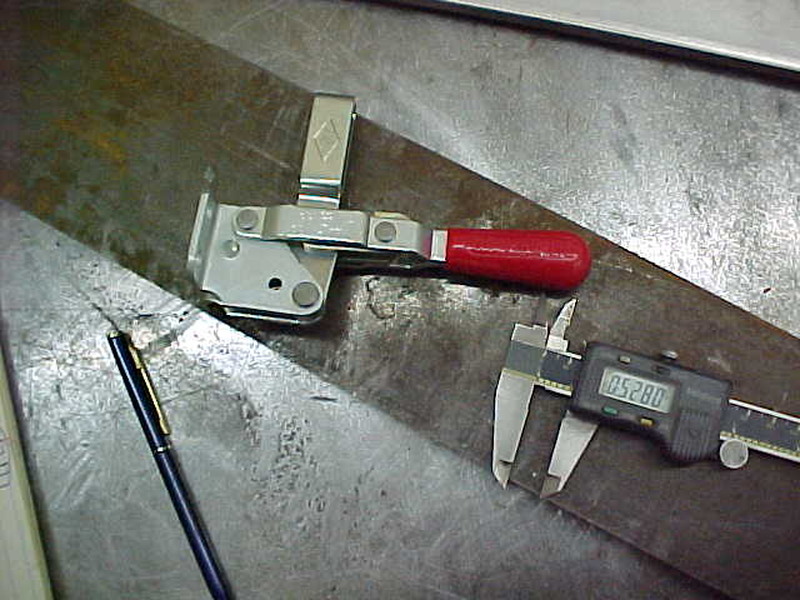
To hold the chain in place I'm planning on a snap clamp. They are adjustable and hold really well.
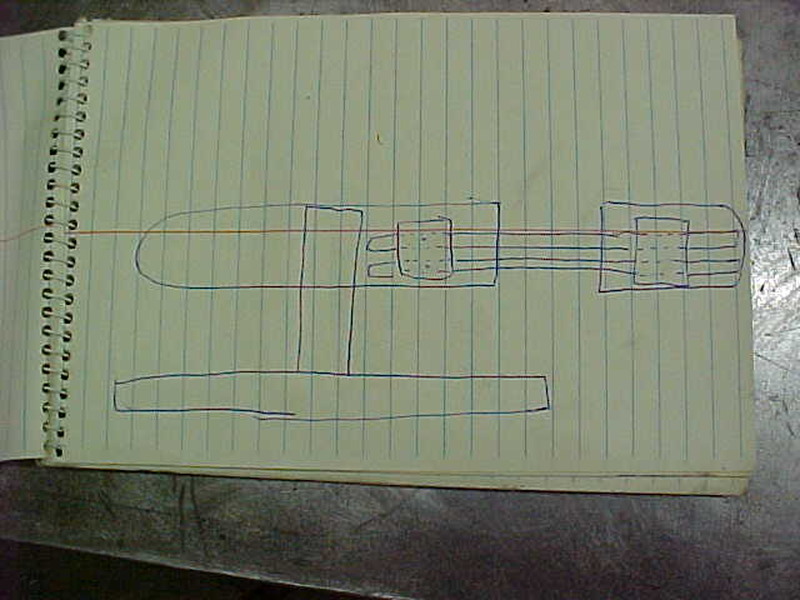
Here's a VERY rough sketch of what's in my head so you have an idea of where I'm trying to go with this
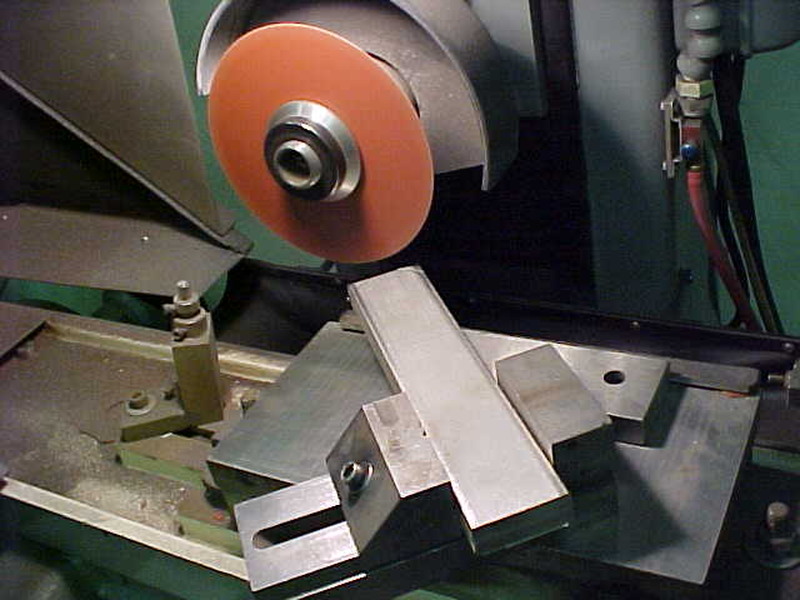
I cut 4 pieces for the chain holder and want to round the ends like a saw bar so the chain doesn't catch. Cut them the same and marked the ends. I threw in on the surface grinder to cut 45 degrees of the excess stock off.
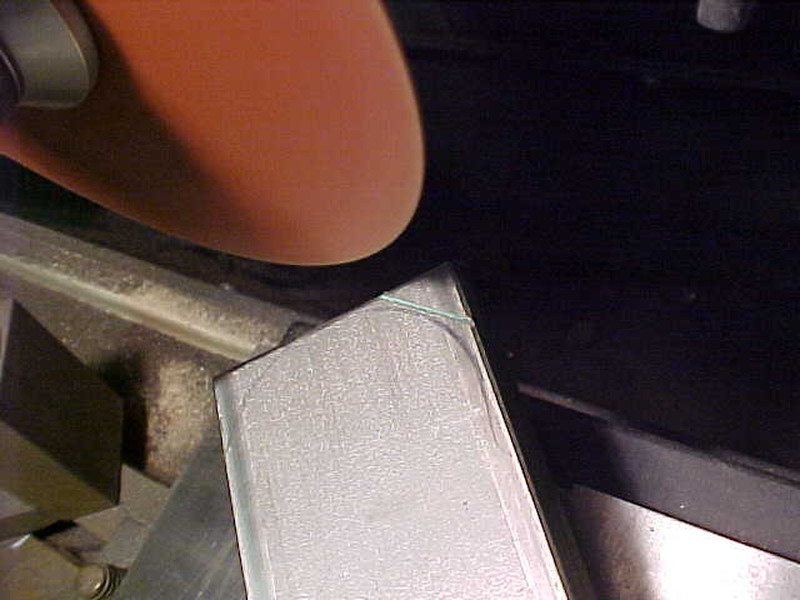
You can get real close and make straight cuts with these.
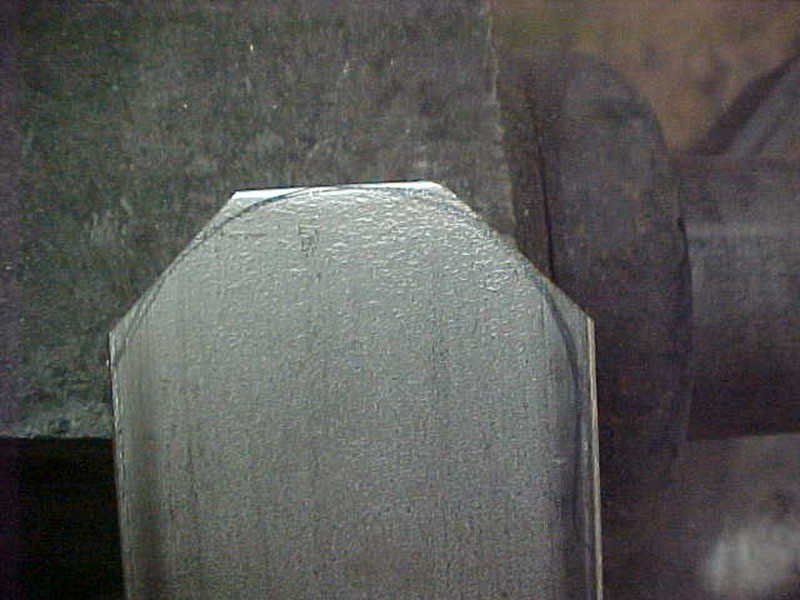
This makes short work for rounding if you don't have a mill like me.
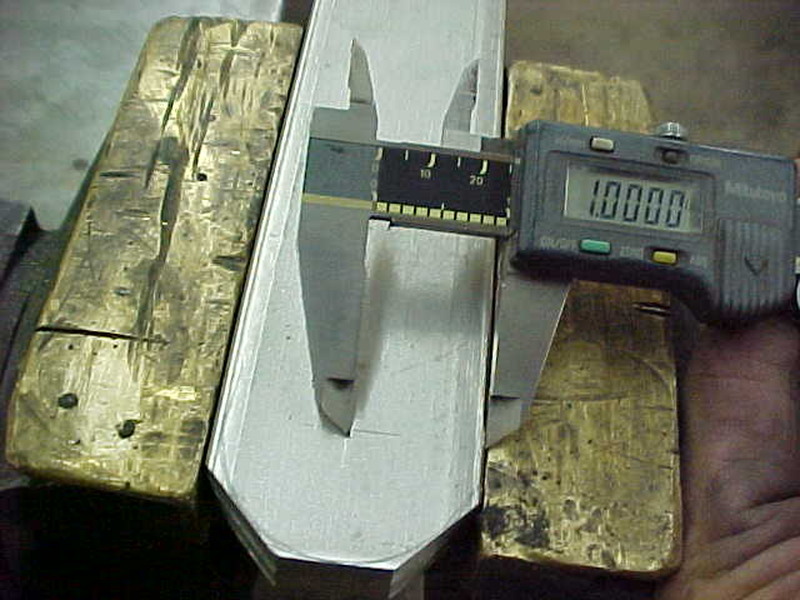
Marked a center hole and I'll do this on both ends. This will hold the together, evenly while I work them up.
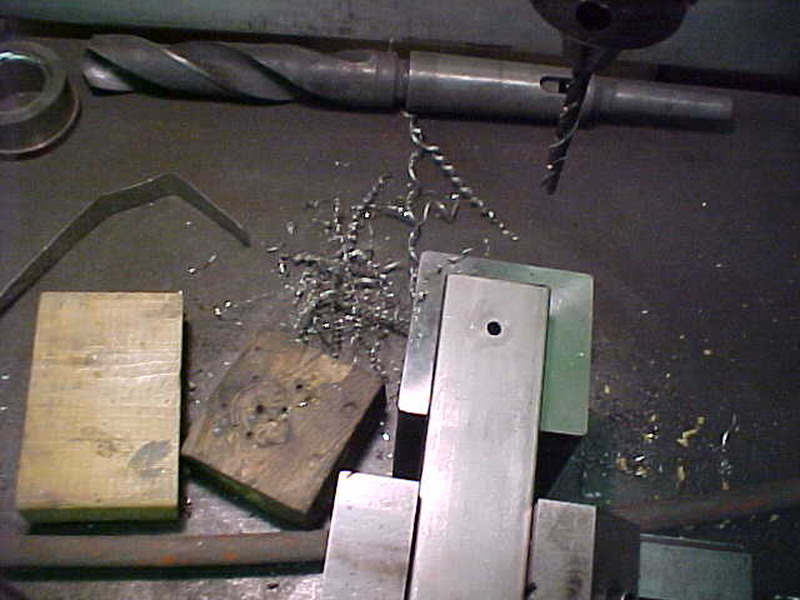
Center drilled and drilled all the holes.