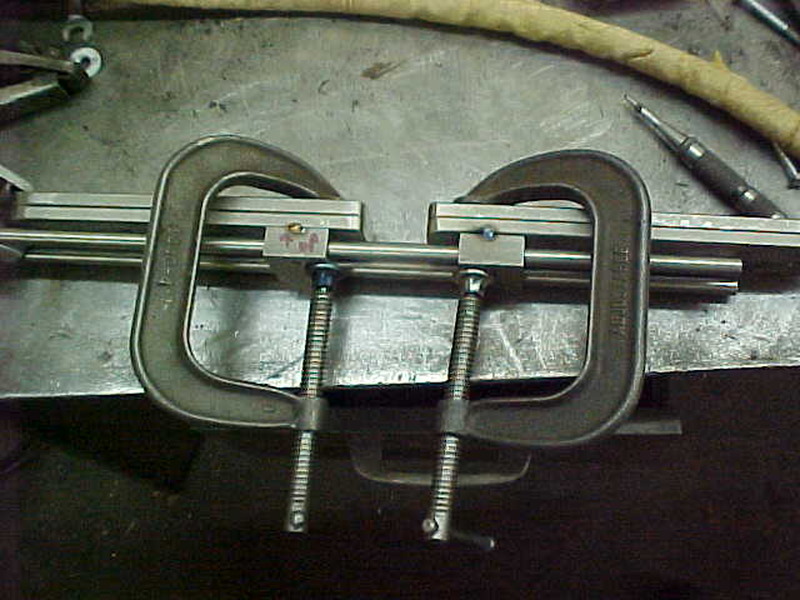
Back to the holders. Clamped it all up on the table and double check to ensure easy movement. I then Tack it and recheck.
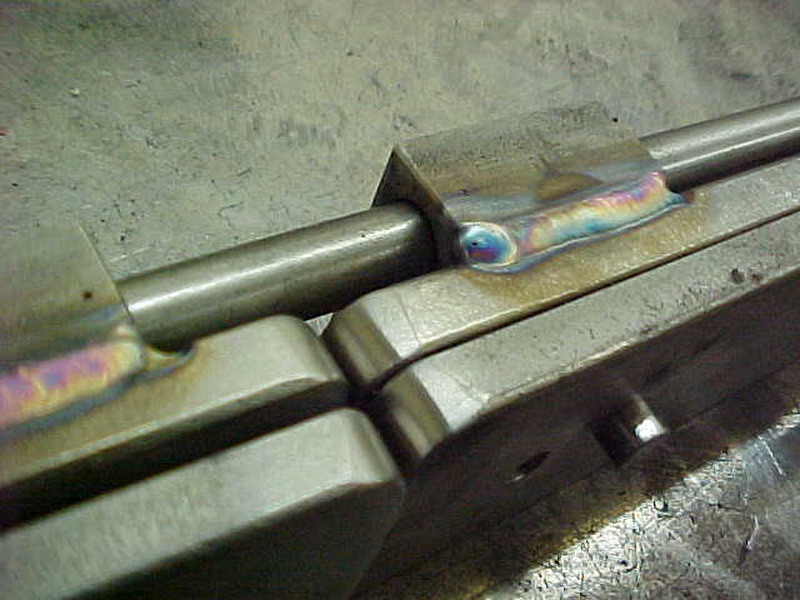
TIG weld it to finish so they are set in place now.
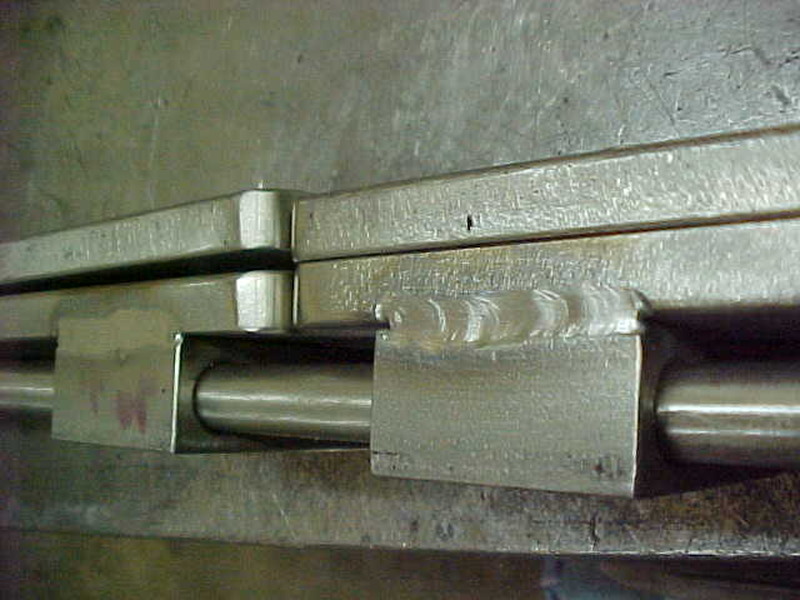
Really like how this is turning out.
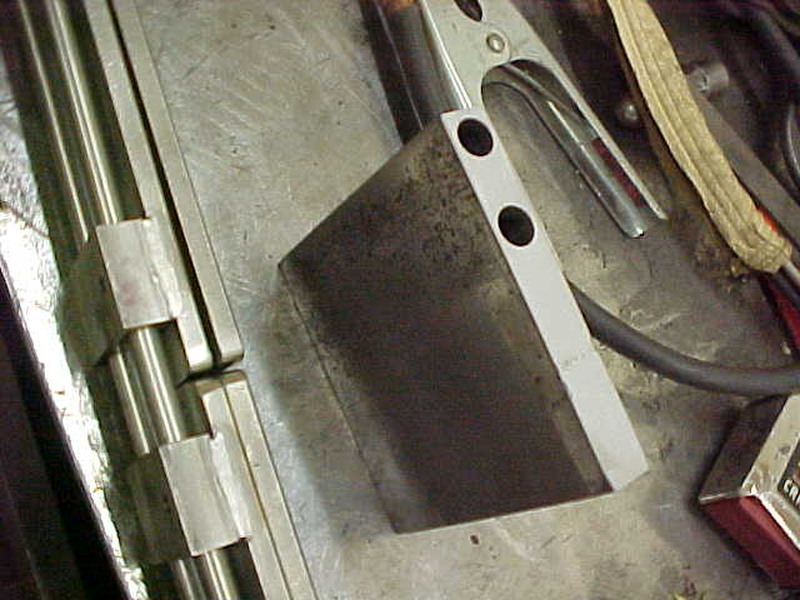
Decided I wanted the upright plate on the same side as the rods. I want the opposite side clear as the clamp needs to be over there. Ended up drilling all the way through the plate for the rods to pass through here when collapsed down, I over sized these top .500
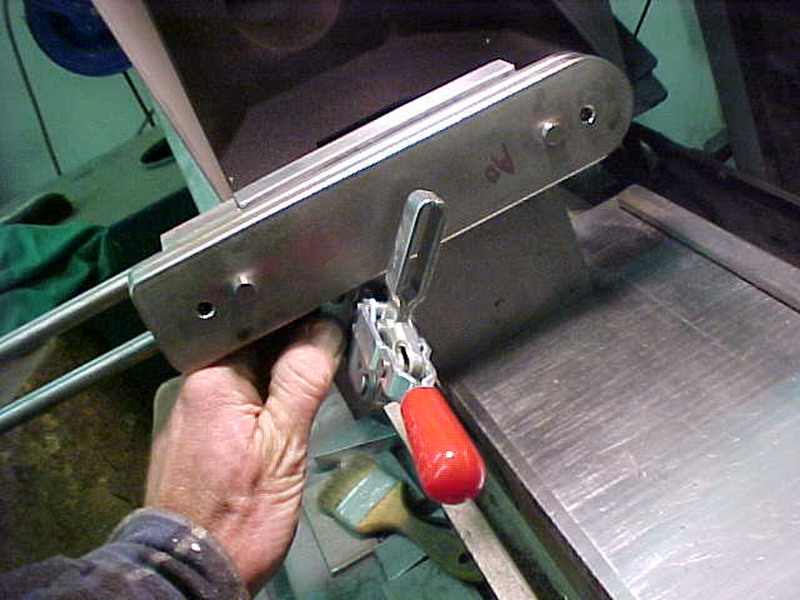
More Mock up. Marking where the clamp will go. I'll drill and tap one hole first and check.
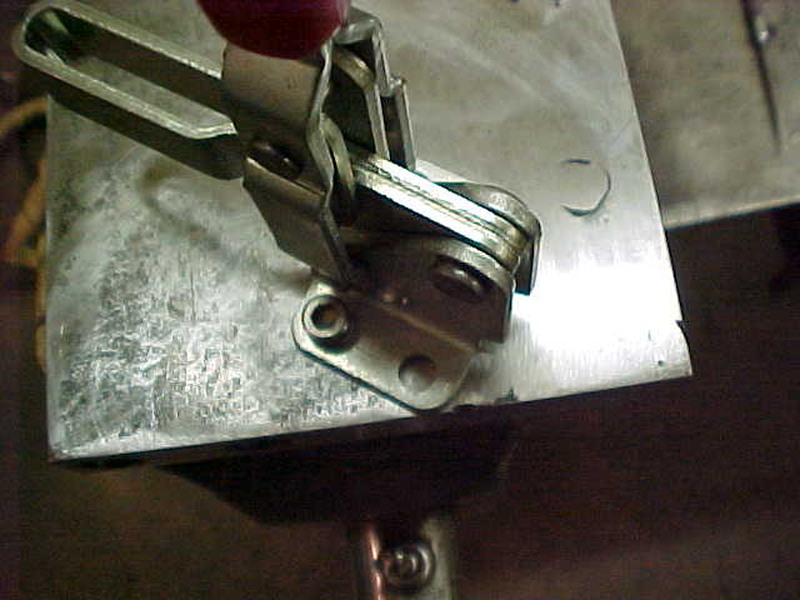
With that done I now have another hand for the final location of the other 3 holes.
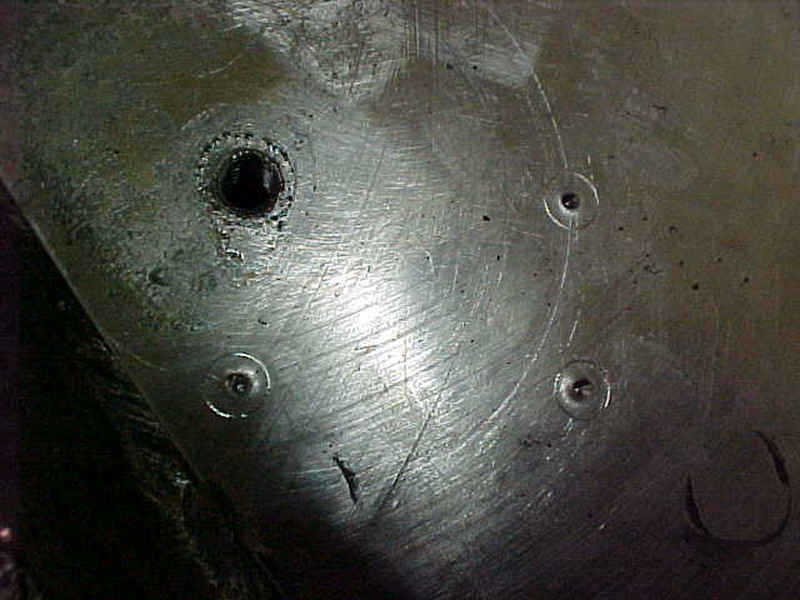
Scribed the circles from the clamps mounting holes and center punch them. I'll drill and tap the rest now.
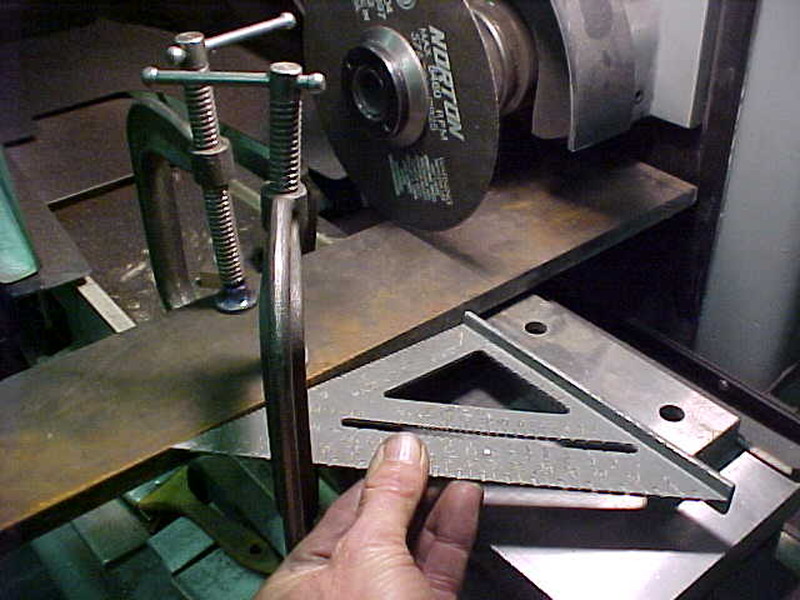
I'll cut the base now. I need it about 7.500 inches long as I want it to overhang the chuck some. This will allow down clearance when the handle releases. Basically a knuckle saver. Using a speed square here to get a nice 90 degree cut.
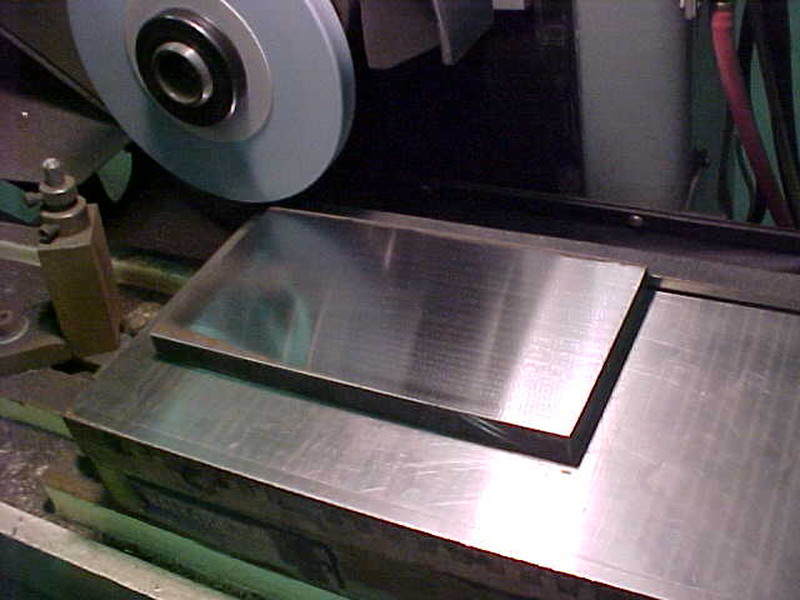
Once cut, I skimmed the bottom of the plate. This is more of a demonstration to prove how much steel moves around when heated /welded on. It took less than .002 of stock removal to get it like this.