Was wanting to fine tune my splitter and find out exactly what the pressure was so I started looking for options. Looked online and found a listing you guys might be interested in too. I ordered them and they seem to work very well. They were right at $20.00 for TWO shipped to my door. Stainless bodies and glycerin filled up to 3000 psi. They have worked so far and helped me out. Here is one installed.
To give you an idea of cost for the fittings, I'm running a 12 JIC(3/4 lines) and the fittings shown were around $35.00. They have an all in one "diagnostic" fitting but it was $45.00 and they had to order it so I went with what is shown. Smaller fittings would be less $ but wanted to give you an estimate on what you're looking at.
I have no affiliation with the seller but here is a link to the gauges.
2 PK 0 3000 PSI 2 5" Hydraulic Air Water Pressure Guage | eBay
For those of you that have gauges on your splitters. I have a shut off from the stand alone unit I used for my tank. Would it be wise to put it on? I'm kinda torn as it's going to make it stick WAY out there but would probably extend the life of the gauge. I may just take the whole thing off too and just put it back on if problems or such arise. Thoughts on what is best???
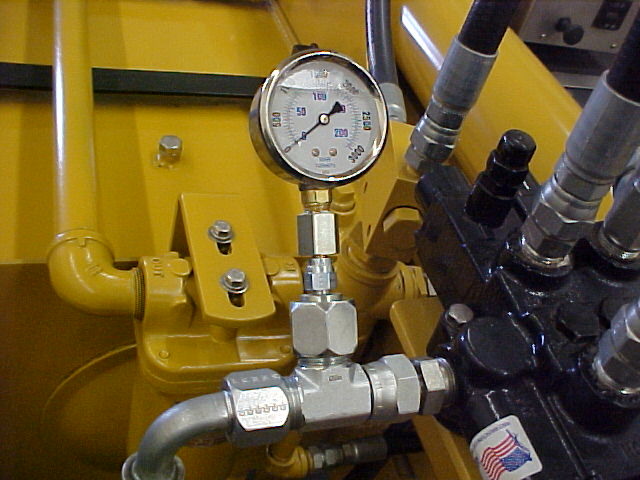
To give you an idea of cost for the fittings, I'm running a 12 JIC(3/4 lines) and the fittings shown were around $35.00. They have an all in one "diagnostic" fitting but it was $45.00 and they had to order it so I went with what is shown. Smaller fittings would be less $ but wanted to give you an estimate on what you're looking at.
I have no affiliation with the seller but here is a link to the gauges.
2 PK 0 3000 PSI 2 5" Hydraulic Air Water Pressure Guage | eBay
For those of you that have gauges on your splitters. I have a shut off from the stand alone unit I used for my tank. Would it be wise to put it on? I'm kinda torn as it's going to make it stick WAY out there but would probably extend the life of the gauge. I may just take the whole thing off too and just put it back on if problems or such arise. Thoughts on what is best???
