Moss Man
Addicted to ArboristSite
I have a firewood log trailer with a grapple loader and when it isn't hooked to the truck it can be a little unstable. The rear of the trailer is all rugged tubular steel and I was thinking if I mounted one Hi-Lift jack on each back corner they could be dropped down for downriggers, you could lightly lift a small amount of weight off the rear and have more stability when loading and unloading while not depending on having the truck hooked up at all times. I load the firewood deck with 2/3rds of a cord at a time and the truck needs to be hooked to the dump trailer under the conveyor while we are running the processor.
Just wondering if anyone has a Hi-Lift and if so, would there be a practical way to mount the jack mechanism to the tube frame of the trailer? I might buy just one jack to look it over, I've been wanting one to have around the farm for some time now.
The trailer looks alot like this one, but it's slightly larger;
Just wondering if anyone has a Hi-Lift and if so, would there be a practical way to mount the jack mechanism to the tube frame of the trailer? I might buy just one jack to look it over, I've been wanting one to have around the farm for some time now.
The trailer looks alot like this one, but it's slightly larger;
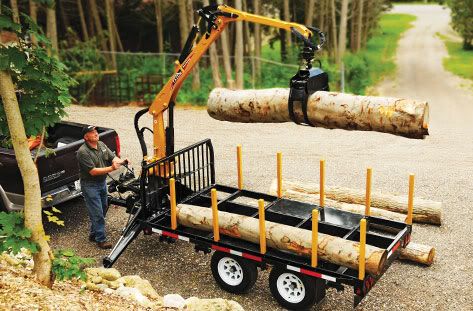
Last edited: